Servo Motor Introduction & Kinetix Selection Guide
Introduction to Servo Motors
Servo Motors are an electro-mechanical device that combines a traditional motor with high precision positioning electronics. The advantage of a servo motor over an inductive motor is the ability to reliably position the motor within a tight tolerance and thus accomplish tasks that one could not with any other motor type.
The electronics that are housed within the “servo motor” are complex. However, there are three main components you should be aware of:
- Servo Drive | Regulates the voltage, communicates with the PLC and the Servo Motor.
- Servo Encoder | The portion of the motor that is responsible for reliably tracking the position of the shaft.
- Servo Motor | The motor that rotates when a voltage is applied.
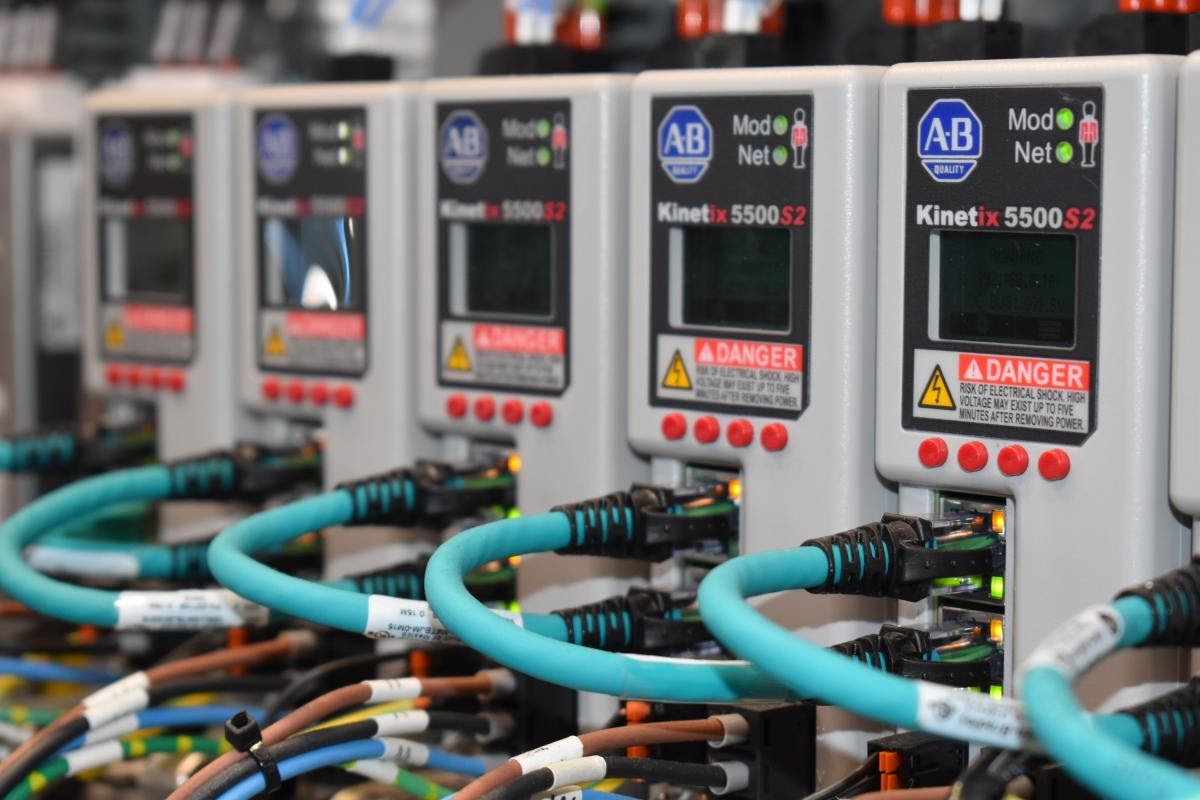
Servo Drive
The servo drive has two main components: low voltage signal processing and high voltage power conversion. The low voltage portion of the drive is responsible for talking with the PLC and processing the encoder information. This portion of the drive will contain parameters, position, sensor data and more. The high voltage portion of the drive will take the input voltage (usually three phase in industrial applications), convert it to DC and create the appropriate voltage at the output. The “appropriate voltage” is dictated by the low voltage portion of the drive.
Servo Encoder
An encoder plays a critical role in a servo system. It tracks the position of the shaft with high accuracy and conveys this information to the controller. The precision or limitation of a specific servo motor is often dictated by the accuracy of the encoder.
Servo Motor
The servo motor is what carries the mechanical load. At the core, the motor is no different from any other motor in the industry. For lighter loads, DC or stepper motors are utilized. For heavier loads, it is preferred to use an induction motor. There are many differences between each motor type and their respective control mechanisms. However, the takeaway is that the motor at the core of a servo system is the same as any other motor you’d encounter in the industry.
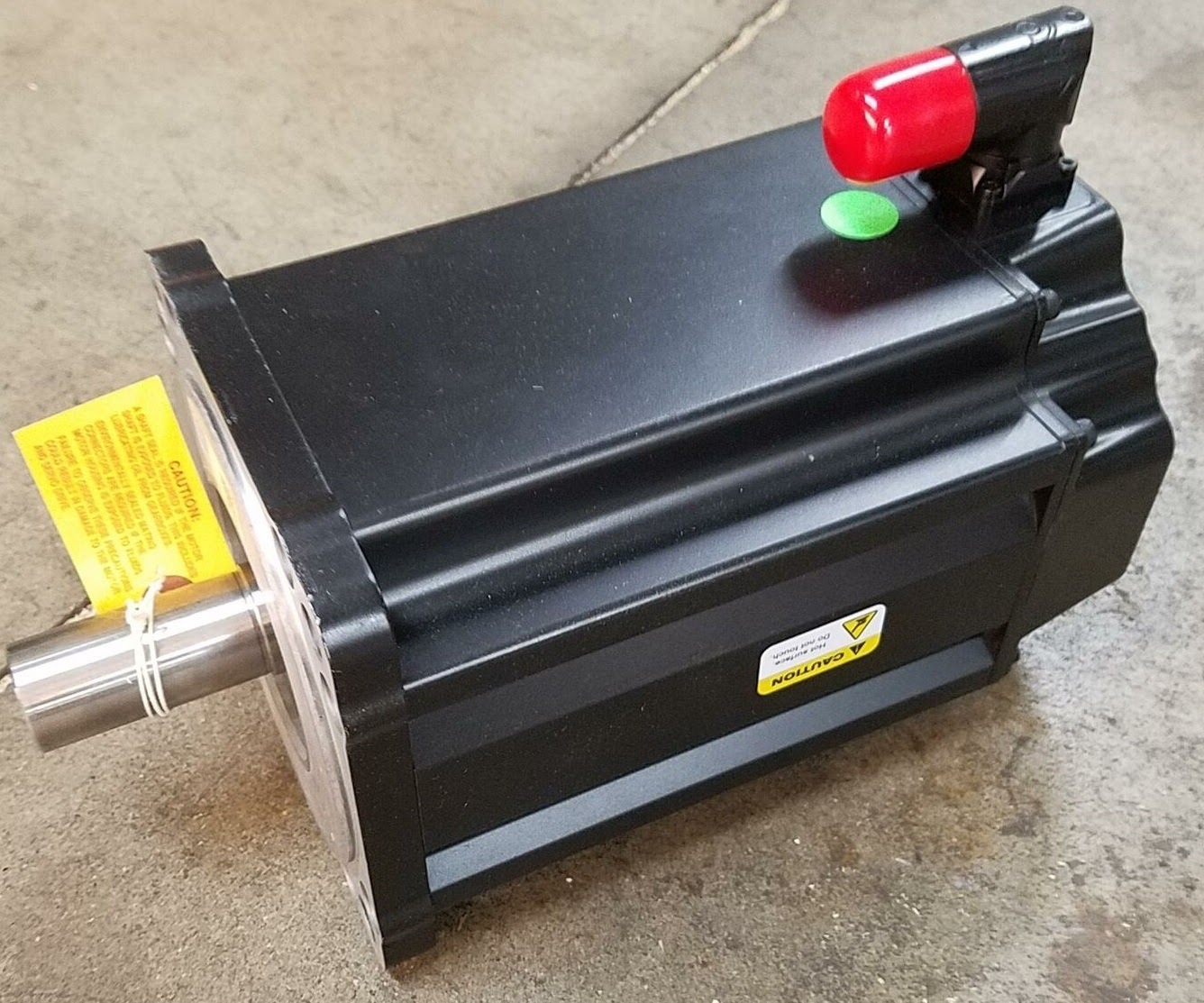
Servo vs Induction Motor
An induction motor is often used to drive pumps, fans, conveyor belts, etc. The reason is that they’re relatively cheap, reliable and capable of driving massive loads. The downside is that it’s difficult to track their position which makes them unusable in accurate positioning applications.
On the opposite side, a servo motor is ideal for high-speed applications, but comes at a much higher cost.
The implementation of a servo system is much more complex than that of an induction motor. A three phase induction motor requires a set of contacts or a frequency drive and little to no programming to get going. On the other hand, servo motion is an entire field within automation and can be quite complex for those to attempt to deploy these systems in the field.
Kinetix Family of Servo Motors
One of the most utilized families of servo motors in North America is the Kinetix from Allen Bradley. It has a direct interface to the CompactLogix and ControlLogix PLCs and easily integrates into the system through RSLogix and Studio 5000 PLC Programming.
As mentioned above, motion control is not a simple process. You need to be familiar with the intricacies of the platform, the various parameters of the system and the hardware choices you must make before undertaking design, upgrade or troubleshooting.
Kinetix Options at a Glance
As of 2021, the supported families of Kinetix stand as follows:
- Kinetix 5700
- Kinetix 5500
- Kinetix 5300
- Kinetix 6500
- Kinetix 350
- Kinetix 6000
- Kinetix 6200
- Kinetix 5100
- Kinetix 300
What are the key differences and what do you need to pay attention to?
Low vs High Axis Count | Depending on the application, you may need a single servo drive or multiple. Based on the families listed above, you can choose one set or the other.
- Low - Kinetix 5500, Kinetix 5300, Kinetix 350, Kinetix 5100, Kinetix 300
- High - Kinetix 5700, Kinetix 6500, Kinetix 6000, Kinetix 6200
Cost & Complexity | Smaller systems with lower resolution requirements should utilize lower end families of servo drives to save on cost.
- Kinetix 5100, Kinetix 300
Safety Rating | Kinetix drives all feature a safety control mechanism. However, they differ between families.
- Category 4 - Kinetix 6500, Kinetix 6200
- Category 3 - Kinetix 5700, Kinetix 5500, Kinetix 350, Kinetix 6000
Motor Compatibility | Every family is compatible with a different set of motors.
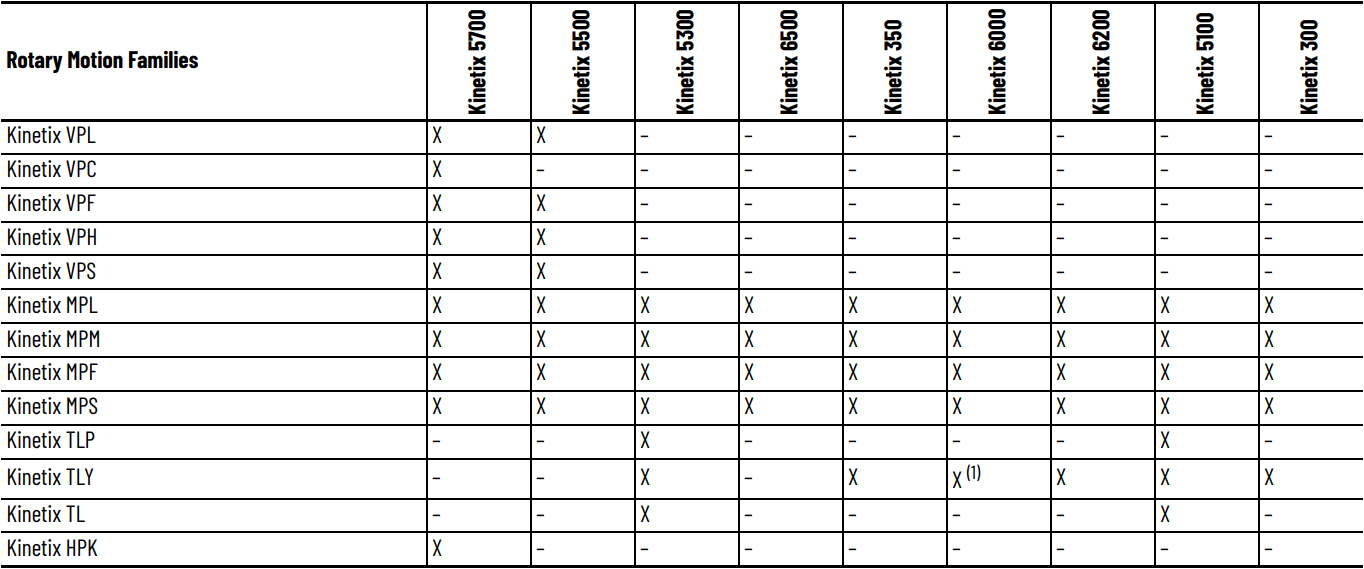
As shown in the table above, reviewing the motors compatible with the drive system is critical in selecting the right drive family. The VP* type motors are only compatible with Kinetix 5700 and Kinetix 5500. If the application at hand requires those motors, the user has no other option than those two families. Similarly, if you require the TL type of motors, you must go with the Kinetix 5300 or Kinetix 5100 systems.
It is also important to note that the table above provides a general overview of Kinetix motor compatibilities. The user must review in depth requirements as every Kinetix motor family may have motors that are or aren’t compatible with the platforms listed above. In other words, even though VPL drives are compatible with Kinetix 5700 and Kinetix 5500 drives, not all motors in the VPL catalog are compatible with each drive.
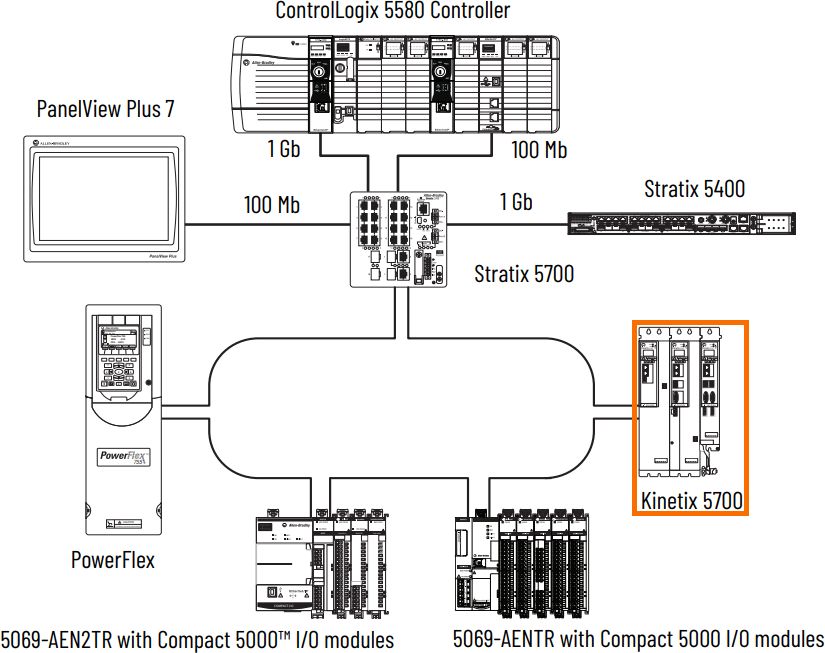
PLC Selection for Motion Control
When it comes to Rockwell PLCs, the keyword for utilizing true servo motion is “CIP Motion”. Certain PLCs will indicate the number of CIP Connections they are capable of supporting. This number will dictate how many servo drivers you can attach to that specific PLC. It’s important to note that certain servo drive systems (lower-end ones) do not support CIP and thus aren’t part of that calculation. However, non-CIP motion will not be as versatile when it comes to RSLogix / Studio 5000 programming.
CIP Motion Capable PLC Systems
CompactLogix
Identifying a CIP capable controller within the CompactLogix family is simple. The suffix will contain the letter “M” in the part number.
- Example: 5069-L306ERM is a CIP motion capable PLC while the 5069-L306ER is not.
The logic above applies to a wide range of PLCs. Below you’ll find several examples of PLCs and the number of axes they support.
- 1769-L18ERM | 2
- 1769-L30ERM | 4
- 1769-L33ERM | 8
As one would imagine, the price of the PLC will increase as the number of supported axes increases.
ControlLogix
The ControlLogix platform PLCs are all capable of CIP motion; some have more axes than others. Unlike CompactLogix, there’s no difference in the part number due to that specific reason.
Servo Motor - Peripherals
Thus far, we’ve covered the major components of the Kinetix platform: drives, motors and PLCs. However, there are a number of peripherals that are required to get the hardware to function beyond what we’ve already covered. These include proprietary connectors and cables.
Due to the unique nature of servo motors and platforms, there is a need to install cabling that is compatible with the drive / motor. In certain cases, the power and low voltage controls are transmitted over a single cable; in others, two cables are required. Although it’s not our intention to cover every variation of cables, it’s important to know that you’ll have to select the correct cable and connector for your drive / motor pair.
Selecting a Servo Motor and Peripherals Process
Step 1 - Establish the mechanical requirements
- Identify where the servo motor will be used. Typically, a mechanical engineer will size the application.
- If uncertain, it’s possible to purchase a drive that will be compatible with a larger motor (in case it has to be upsized).
Step 2 - Choose the right motor
- From the Kinetix family of motors, select the one that is appropriate for your application.
- Note: Rockwell provides a range of specially servo motors. Ex: the washdown safe motors are preferred when working in a food & bev environment that will be exposed to water.
Step 3 - Choose the drive
- Based on the motor you have selected in “Step 2”, choose the appropriate drive based on the variations we described in the previous section.
- Note: In addition to choosing the right drive, we recommend that our clients spend the time to identify future needs. In other words, we may recommend that you choose a drive platform that can be expanded based on system needs in the future.
Step 4 - Choose peripherals (PLC / Cables / Connectors)
- Based on the drive and motor, either identify the PLC that will execute motion commands or choose one to purchase.
- Identify the cables and connectors required for the system.
Conclusion on Servo Motors
Servo Motors are used in industrial applications where accuracy in positioning is required. They provide a level of control that is impossible to achieve with any other motor type. However, they do come at a premium cost and integration time.
An Allen Bradley servo motion platform is Kinetix. Kinetix provides a variety of drives and motors for a wide number of different applications. Based on customer needs, a systems integrator can choose the right motor and drive.