The Ultimate Guide to PLC Training: Skills, Certifications, and Future Trends in Industrial Automation
Introduction to PLCs
Definition and Role of PLCs in Industrial Automation
A Programmable Logic Controller (PLC) is an industrial-grade computer designed to automate electromechanical processes in manufacturing and production environments. Unlike general-purpose computers, PLCs are built to withstand harsh industrial conditions, including extreme temperatures, humidity, and electrical noise. They play a crucial role in controlling machinery, assembly lines, robotic systems, and industrial processes by executing programmed logic in real time.
At their core, PLCs operate based on inputs, logic processing, and outputs. Inputs can come from sensors, switches, or other field devices that detect conditions like temperature, pressure, or the position of a component. The PLC then processes these signals using a program, typically written in Ladder Logic, Structured Text, or Function Block Diagram (FBD). Once the logic executes, the PLC sends output signals to actuators, motors, valves, and other control elements, ensuring that industrial operations run smoothly and efficiently.
PLCs are widely used across industries such as automotive, food and beverage, pharmaceutical, oil and gas, and power generation. They enable automation by reducing human intervention, improving efficiency, minimizing errors, and enhancing safety. In modern manufacturing, PLCs are also integral to smart factory initiatives, facilitating data collection, integration with SCADA (Supervisory Control and Data Acquisition) systems, and connectivity with higher-level IT systems like Manufacturing Execution Systems (MES) and Enterprise Resource Planning (ERP) platforms.
Leading PLC manufacturers include Siemens, Rockwell Automation (Allen-Bradley), Mitsubishi Electric, Schneider Electric, and Omron, each offering a range of PLC solutions catering to different industrial needs. For example, Siemens' SIMATIC S7 series is widely used in European industries, while Rockwell Automation's ControlLogix and CompactLogix PLCs dominate North American manufacturing.
Historical Evolution of PLCs and Their Impact on Manufacturing
The development of PLC technology dates back to the late 1960s, when manufacturing industries sought a more efficient alternative to hardwired relay-based control systems. Before PLCs, industrial automation relied on mechanical relays and complex wiring, which were difficult to modify, troubleshoot, and scale.
The first PLC, Modicon 084, was developed in 1968 by Dick Morley, often regarded as the "father of the PLC." This invention revolutionized industrial automation by replacing traditional relay logic with software-based programming, allowing engineers to reprogram processes without rewiring control panels. The introduction of PLCs led to a significant reduction in system complexity, increased production uptime, and streamlined maintenance.
During the 1980s and 1990s, PLCs evolved with the advent of programmable memory, networking capabilities, and standardized programming languages. The adoption of IEC 61131-3, an international standard defining PLC programming languages, further improved interoperability and simplified engineering workflows.
The 21st century has seen PLCs integrating with Industrial Internet of Things (IIoT), cloud computing, and edge computing to support smart manufacturing. Modern PLCs, such as Siemens S7-1500, Allen-Bradley CompactLogix, and Beckhoff's TwinCAT, now feature Ethernet/IP, PROFINET, and OPC UA for seamless communication with enterprise systems, enabling real-time monitoring, predictive maintenance, and data-driven decision-making.
The impact of PLCs on manufacturing has been profound. Companies leveraging PLC-based automation have seen higher production efficiencies, lower operational costs, improved product quality, and enhanced safety compliance. PLCs have also played a critical role in the rise of flexible manufacturing systems (FMS), allowing factories to quickly adapt to changing production demands.
Today, as industries move toward Industry 4.0, PLCs are evolving further with integrated cybersecurity features, cloud-based programming environments, and AI-driven analytics. With advancements such as Siemens’ TIA Portal, Rockwell Automation’s FactoryTalk, and Beckhoff’s TwinCAT 3, PLCs are no longer just controllers but central hubs for industrial data processing and decision-making.
The next section will explore the importance of PLC training, discussing why engineers, technicians, and operators must develop strong PLC skills to keep pace with technological advancements and industrial automation demands.
Importance of PLC Training
The Necessity of PLC Proficiency for Engineers and Technicians
As industrial automation continues to evolve, PLC proficiency has become a critical skill for engineers, technicians, and maintenance personnel. Manufacturing facilities rely on PLCs to control automated processes, optimize production, and ensure operational efficiency. However, the effectiveness of these systems depends largely on the expertise of the individuals who program, troubleshoot, and maintain them.
For engineers, PLC knowledge is essential for designing and implementing automation solutions. A strong understanding of PLCs enables them to develop efficient control logic, integrate industrial networks, and optimize machine performance. Engineers working in manufacturing, oil and gas, pharmaceuticals, automotive, food and beverage, and logistics frequently encounter PLCs from major OEMs such as Siemens, Rockwell Automation (Allen-Bradley), Mitsubishi, Schneider Electric, and Omron. Each manufacturer has distinct programming environments—Siemens uses TIA Portal, Rockwell Automation uses Studio 5000, and Mitsubishi uses GX Works—requiring engineers to be proficient in multiple platforms.
For technicians and maintenance personnel, PLC expertise is crucial for troubleshooting and ensuring minimal downtime. In industrial environments, machine failures can lead to costly production losses. A well-trained technician can quickly diagnose issues, modify PLC code when necessary, and restore operations efficiently. Understanding Ladder Logic, Function Block Diagrams (FBD), and Structured Text (ST) allows technicians to interpret control programs and make necessary adjustments without the need for external consultants.
Additionally, many companies now require PLC proficiency as a core skill for hiring and promotions. Job postings for automation engineers, controls engineers, and maintenance technicians frequently list PLC programming and troubleshooting as mandatory qualifications. As automation technology advances, the demand for skilled PLC professionals will continue to grow, making formal training a valuable investment for career development.
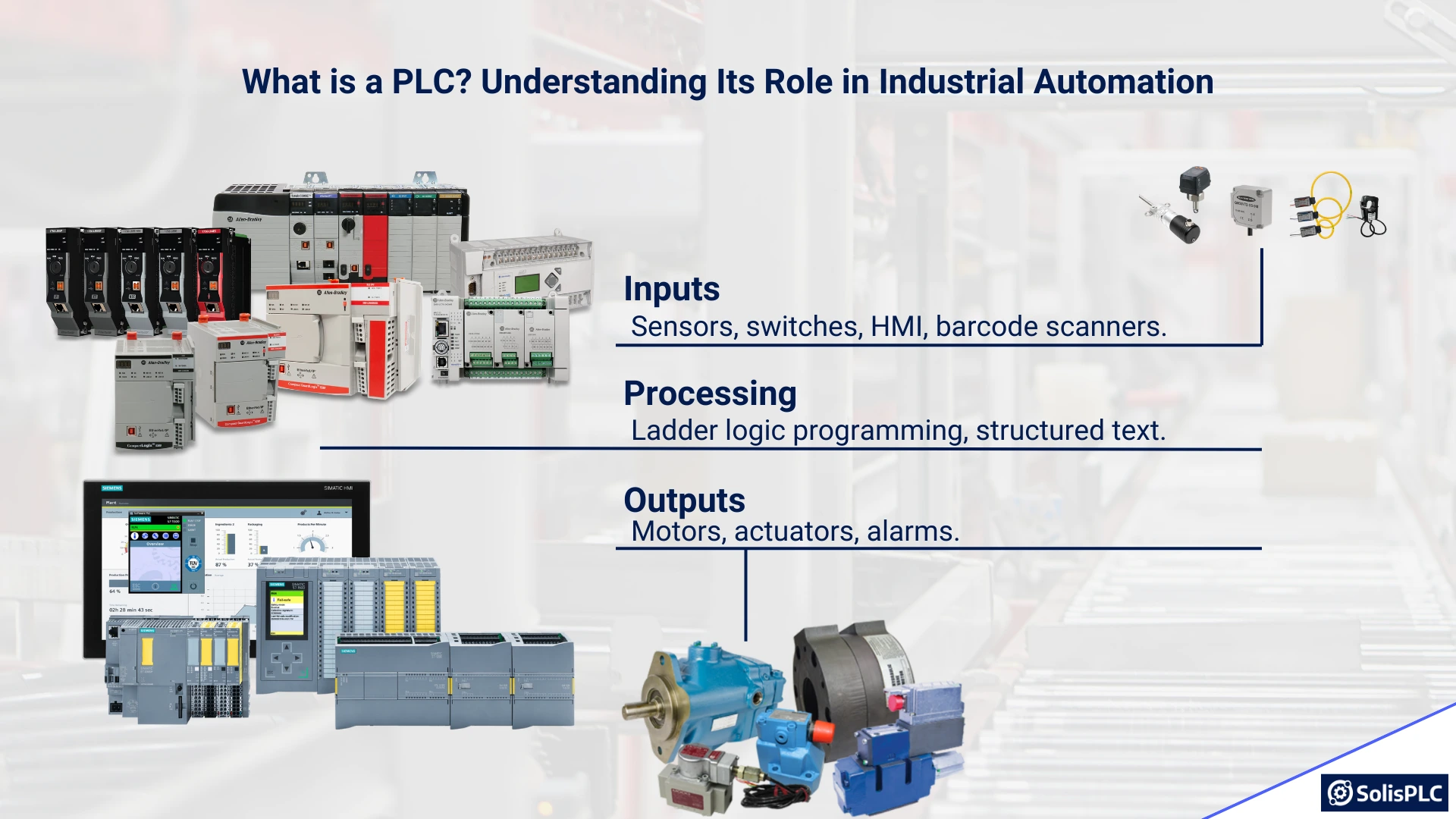
Benefits of Formal PLC Training in Enhancing Operational Efficiency and Safety
While some professionals gain PLC skills through on-the-job experience, structured training programs provide a more comprehensive and efficient learning approach. Formal training ensures that individuals receive instruction on both fundamental programming concepts and advanced industrial applications.
- Reduced Machine Downtime and Faster Troubleshooting
A common challenge in industrial environments is unexpected machine failures. Without proper training, diagnosing PLC-related issues can be time-consuming and may require external support. A technician trained in PLC troubleshooting can quickly analyze error codes, modify logic, and restore system functionality, significantly reducing unplanned downtime. - Improved Safety in Industrial Automation
Improper PLC programming or a lack of troubleshooting skills can lead to hazardous conditions, including unexpected machine movements, electrical hazards, or emergency stop failures. Formal PLC training emphasizes best practices in programming safety logic, integrating safety relays, and working with fail-safe PLCs such as Siemens’ S7-1200F or Allen-Bradley’s GuardLogix. Training also covers compliance with international safety standards like ISO 13849 and IEC 61508, ensuring that automation professionals design systems that prioritize worker safety. - Higher Production Efficiency and Quality Control
A well-trained workforce can optimize PLC programming for improved cycle times, energy efficiency, and production consistency. Advanced training covers PID (Proportional-Integral-Derivative) control, motion control, and data logging, enabling engineers to fine-tune automation processes for higher efficiency. For example, a trained PLC programmer can implement real-time process adjustments to reduce scrap rates in manufacturing or optimize conveyor belt speeds in logistics operations. - Better Integration with Industry 4.0 and Smart Manufacturing
Modern industrial automation is moving towards Industry 4.0, IIoT (Industrial Internet of Things), and cloud-based automation. Engineers with PLC training can integrate control systems with SCADA (Supervisory Control and Data Acquisition), MES (Manufacturing Execution Systems), and cloud analytics platforms. PLC training courses that include OPC UA, MQTT, and Industrial Ethernet help professionals prepare for future-ready automation environments. - Career Advancement and Job Security
Companies are increasingly investing in automation-driven cost reduction and efficiency improvements, leading to a higher demand for professionals with PLC skills. Engineers and technicians who complete formal PLC training programs can command higher salaries, access better job opportunities, and transition into leadership roles within automation and control system engineering. A 2023 industry report by the International Society of Automation (ISA) found that PLC-skilled engineers earn up to 25% more than their counterparts without formal training. - Access to Vendor-Specific Expertise
Many leading automation companies offer certified PLC training programs that provide specialized knowledge tailored to their platforms. For instance:- Siemens TIA Portal training ensures engineers can program and troubleshoot S7-1200 and S7-1500 PLCs effectively.
- Rockwell Automation’s Studio 5000 training equips learners to work with ControlLogix and CompactLogix PLCs.
- Mitsubishi Electric’s GX Works training helps professionals develop expertise in FX and Q Series PLCs.
By obtaining vendor-specific training, automation professionals increase their job prospects and improve their ability to work with global manufacturers.
Conclusion
PLC training is no longer optional for engineers and technicians in industrial automation—it is a necessity. As manufacturing systems become more complex and interconnected, having a workforce skilled in PLC programming, troubleshooting, and optimization leads to higher efficiency, reduced downtime, enhanced safety, and better overall plant performance.
In the next section, we will explore the various types of PLC training programs, including online courses, in-person workshops, and industry certifications, helping professionals choose the best path for their skill development.
Types of PLC Training Programs
PLC training programs are available in various formats to cater to different learning preferences, career goals, and industrial requirements. From self-paced online courses to hands-on workshops and structured academic programs, each type of training offers unique benefits. Understanding these options allows engineers, technicians, and automation professionals to select the best path for developing their PLC expertise.
Online PLC Training Courses
Online PLC courses have gained popularity due to their flexibility, affordability, and accessibility. These courses allow learners to progress at their own pace, making them ideal for working professionals who need to upskill without disrupting their jobs. Many online platforms provide video-based lessons, interactive simulations, and downloadable PLC programming exercises, enabling hands-on learning without requiring expensive hardware.
Advantages of Online PLC Training:
- Flexible learning – Study at your own pace from anywhere in the world.
- Lower cost compared to in-person courses.
- Access to instructor-led explanations and lifetime course materials.
- Simulations and virtual PLC environments reduce the need for physical hardware.
Recommended Online PLC Training Providers:
- SolisPLC
- SolisPLC offers a comprehensive collection of PLC courses designed for beginners, intermediate learners, and advanced automation professionals.
- Courses cover Allen-Bradley (Studio 5000, RSLogix 500), Siemens (TIA Portal), and HMI/SCADA systems.
- One notable course is “Siemens TIA Portal – Intermediate PLC Programming”, which provides a detailed breakdown of function blocks, data blocks, and communication protocols used in Siemens automation.
- Website: solisplc.com
- Udemy (Vladimir Romanov’s PLC Courses)
- Vladimir Romanov, a recognized industry expert, has developed highly rated Udemy courses focusing on RSLogix 500 & 5000 (Allen-Bradley), FactoryTalk View (HMI), and advanced PLC programming techniques.
- The “PLC Programming - Training from Scratch on RSLogix500 & 5000” course helps learners build real-world ladder logic programs, understand I/O configurations, and design basic HMI screens.
- Other Online Learning Platforms
- LinkedIn Learning and Pluralsight also offer introductory PLC courses, but they may not be as in-depth as specialized platforms like SolisPLC or Joltek.
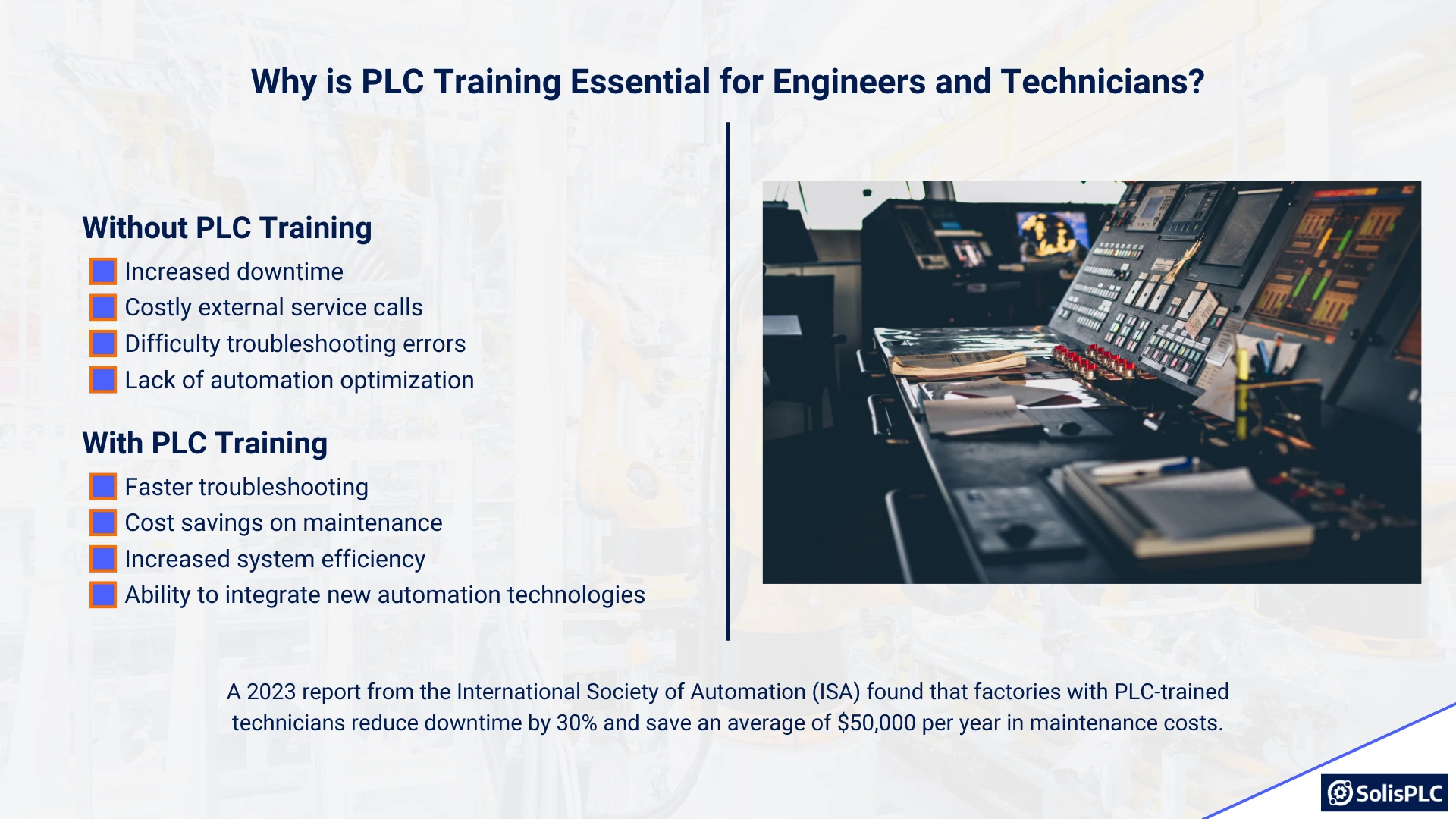
Who Should Choose Online PLC Training?
- Engineers and technicians looking for self-paced training.
- Professionals seeking affordable alternatives to in-person classes.
- Individuals who prefer learning through video tutorials and simulations.
In-Person PLC Workshops
While online training provides convenience, in-person workshops offer hands-on experience with real PLC hardware. These workshops are typically hosted by technical colleges, industrial training centers, and automation vendors.
Advantages of In-Person PLC Training:
- Direct access to physical PLC equipment for real-world programming.
- Live troubleshooting exercises to simulate plant conditions.
- Instructor-led support and networking opportunities.
Where to Find In-Person PLC Training?
- Local Technical Colleges and Universities
- Many technical institutes offer short-term PLC training workshops as part of their continuing education programs.
- Example: George Brown College (Canada) and Pennsylvania College of Technology (USA) provide hands-on PLC courses.
- Automation Vendors (OEM Training Programs)
- Leading automation manufacturers provide certified PLC training on their specific platforms:
- Siemens TIA Portal Training – Siemens offers factory training for S7-1200 and S7-1500 PLCs.
- Rockwell Automation (Allen-Bradley) Training – Rockwell Automation provides in-person workshops on Studio 5000, ControlLogix, and CompactLogix.
- Mitsubishi and Omron also offer vendor-specific training programs.
- Leading automation manufacturers provide certified PLC training on their specific platforms:
- Industrial Training Centers
- Some private automation training centers specialize in PLC boot camps and factory floor applications.
Who Should Choose In-Person PLC Training?
- Technicians and maintenance personnel who need hands-on experience.
- Engineers working in highly regulated industries (pharma, oil & gas, automotive, etc.) where vendor certification is required.
- Companies investing in employee upskilling to reduce PLC-related downtime.
Certificate and Diploma Programs
For individuals seeking formal education in PLCs, certificate and diploma programs provide structured coursework in industrial automation, PLC programming, and control systems engineering. These programs are typically longer in duration than short-term workshops and may be offered by universities, community colleges, and technical schools.
Advantages of PLC Certificate & Diploma Programs:
- Provides industry-recognized credentials.
- Covers fundamentals to advanced PLC applications.
- May include internships or co-op programs with industrial partners.
- Often taught by experienced engineers and industry professionals.
Examples of Certificate & Diploma Programs:
- George Brown College (Canada) – Offers an online PLC Technician Certificate Program that includes hands-on labs and interactive simulations.
- Penn State University (USA) – Provides continuing education programs in PLC programming and industrial automation.
- University of Sheffield (UK) – Features a control systems engineering diploma that includes PLC coursework.
Who Should Choose Certificate & Diploma Programs?
- Individuals looking for formal credentials in industrial automation.
- Engineering students and career changers seeking PLC-related job opportunities.
- Professionals aiming for management roles in automation and controls.
Choosing the Right PLC Training Program
For professionals looking to gain practical, job-ready skills, online courses offer the best flexibility. Meanwhile, those working with specific brands like Siemens, Rockwell, or Mitsubishi should consider vendor-certified training.
Conclusion
PLC training comes in many forms, each with its advantages and target audience. Online courses provide flexibility, in-person workshops offer hands-on experience, and formal certificate programs deliver industry-recognized credentials. Selecting the right program depends on career goals, budget, and learning preferences.
In the next section, we will dive deeper into the key components of effective PLC training, including programming languages, troubleshooting skills, and real-world case studies.
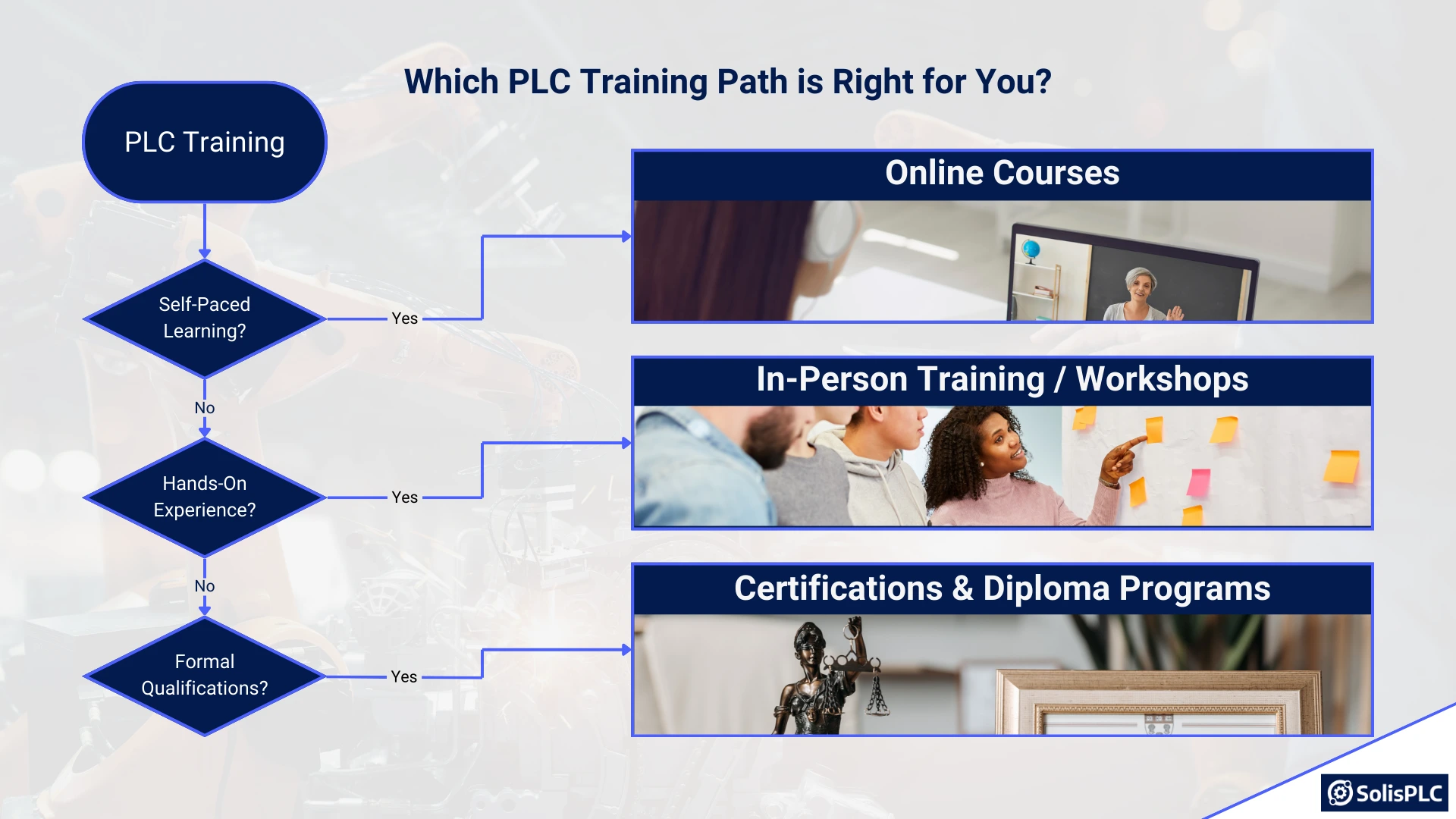
Key Components of Effective PLC Training
PLC training is most effective when it goes beyond theoretical knowledge and incorporates practical applications, hands-on troubleshooting, and exposure to real-world industrial scenarios. For professionals in automation, a well-rounded PLC training program should include various programming languages, familiarity with multiple hardware and software platforms, problem-solving skills, and case studies that reflect real manufacturing challenges.
Understanding Different PLC Programming Languages
A critical component of PLC training is understanding the various programming languages used to develop control logic. The IEC 61131-3 standard defines five primary PLC programming languages, but the most widely used are:
- Ladder Logic (LD)
- The most common and widely adopted PLC programming language, especially in North America.
- Originally developed to mimic relay logic diagrams, making it easier for electrical engineers and maintenance technicians to understand.
- Used in Allen-Bradley Studio 5000, Siemens TIA Portal, and Schneider Electric’s EcoStruxure.
- Strengths: Easy visualization, widely supported, quick troubleshooting.
- Example: A simple motor start/stop circuit with interlocks.
- Structured Text (ST)
- A high-level programming language similar to Pascal or C.
- Preferred for complex mathematical operations, batch processing, and data handling.
- Found in Siemens TIA Portal, Beckhoff TwinCAT (Codesys), and Omron CX-One.
- Strengths: Efficient for advanced logic, data manipulation, and integration with databases.
- Example: A PID control loop or a recipe-based batch system.
- Function Block Diagram (FBD)
- A graphical representation of functions and logic.
- Commonly used in process automation and motion control.
- Found in Siemens, ABB, and Schneider Electric platforms.
- Strengths: Easier visualization for modular programming.
- Example: Implementing a temperature control system.
- Sequential Function Chart (SFC)
- Designed for state-based and sequential operations.
- Often used in robotics, automated assembly lines, and batch processing.
- Strengths: Simplifies step-by-step processes like machine sequencing.
- Example: Programming a conveyor system with different stages.
- Instruction List (IL) (Legacy)
- A low-level programming language similar to assembly language.
- Less commonly used in modern PLCs due to Structured Text's efficiency.
Why Multi-Language Training Matters
A strong PLC training program should cover multiple languages, allowing engineers and technicians to:
- Work with different PLC brands that support specific programming standards.
- Develop optimized logic based on the application’s complexity.
- Improve troubleshooting skills across various programming environments.
Familiarity with Various PLC Hardware and Software Platforms
To be effective, PLC training must expose learners to multiple manufacturers’ hardware and software. This ensures that automation professionals can adapt to different industrial environments and work on diverse projects.
Major PLC Brands and Their Software Environments

Why Cross-Platform Training is Essential
- Flexibility in industrial projects – Different factories and industries use different PLC brands.
- Improved troubleshooting skills – Knowing multiple platforms helps engineers debug and modify programs across various plants.
- Higher employability – Multi-brand expertise makes engineers more valuable in the job market.
Most PLC training programs start with one manufacturer’s ecosystem (such as Allen-Bradley or Siemens) before expanding into multi-brand knowledge.
Emphasis on Troubleshooting and Problem-Solving Skills
The ability to diagnose and resolve PLC-related issues is one of the most valuable skills for engineers and technicians. Effective PLC training should include real-world troubleshooting exercises to help learners develop critical problem-solving skills.
Key Troubleshooting Topics in PLC Training
- Understanding Fault Codes & Error Messages
- Siemens PLCs provide diagnostic buffer logs in TIA Portal.
- Allen-Bradley PLCs display fault codes in RSLogix 5000.
- Mitsubishi PLCs use error monitoring in GX Works3.
- Identifying Communication Issues
- Troubleshooting Ethernet/IP, PROFINET, and Modbus TCP/IP networks.
- Diagnosing I/O failures, sensor disconnections, and noise interference.
- Debugging Ladder Logic and Program Execution
- Using step-by-step debugging tools in Studio 5000 and TIA Portal.
- Simulating logic to detect issues before deploying to live machinery.
- Handling Emergency Stop (E-Stop) and Safety PLC Issues
- Understanding fail-safe PLCs (S7-1500F, GuardLogix).
- Troubleshooting safety interlocks and redundant circuits.
- Testing & Validation with PLC Simulators
- Siemens TIA Portal PLCSIM and Allen-Bradley’s Emulate 5000 allow engineers to test logic without real hardware.
- Online training platforms like SolisPLC and Joltek provide virtual PLC environments for learning.
Integration of Real-World Applications and Case Studies
The best PLC training programs include hands-on applications that mirror real industrial scenarios. These case studies help engineers and technicians apply their knowledge in practical automation projects.
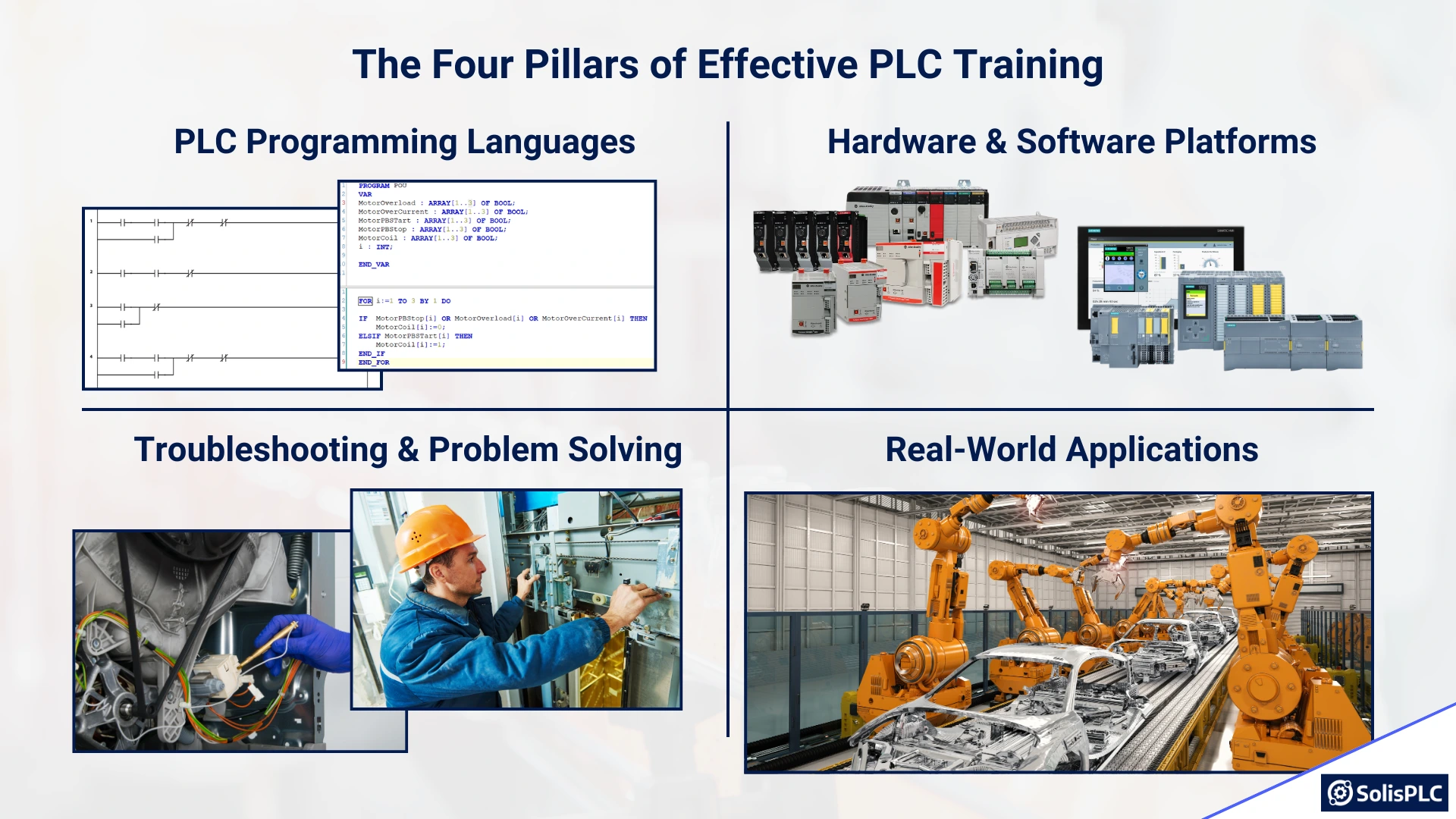
Example Case Studies in PLC Training
- Conveyor System Automation
- Programming a variable-speed conveyor with sensors and diverters.
- Implementing fault handling and emergency stops.
- PID Control for Temperature Regulation
- Using Siemens S7-1500 to control a heating system.
- Configuring PID loops for smooth temperature adjustments.
- Packaging Line with Robotics & Motion Control
- Controlling a robotic pick-and-place system using Beckhoff TwinCAT.
- Integrating Servo Drives and Stepper Motors in an automated packing station.
- SCADA & HMI Integration
- Building an HMI screen with FactoryTalk View or WinCC.
- Displaying real-time data and alarms for an industrial process.
- Data Logging & IIoT Connectivity
- Collecting sensor data and sending it to cloud-based analytics.
- Using MQTT and OPC UA for industrial communication.
Why Real-World Training Matters
- Bridges the gap between theory and practice.
- Prepares learners for real industrial projects.
- Helps with job placement and career advancement.
Conclusion
An effective PLC training program must go beyond the basics and prepare learners for real-world industrial automation challenges. This includes: âś” Learning multiple programming languages to handle diverse logic requirements.
âś” Becoming proficient with various PLC brands and software platforms.
âś” Mastering troubleshooting techniques to reduce downtime in industrial environments.
âś” Applying knowledge to real-world case studies and industrial automation projects.
By focusing on these key components, engineers and technicians can develop the skills necessary to excel in the automation industry.
In the next section, we will explore global perspectives on PLC training, including how different regions (North America, Europe, and Asia) approach industrial automation education.
Global Perspectives on PLC Training
PLC training is essential worldwide as industries continue to embrace automation and digital transformation. However, the approach to PLC education varies by region, influenced by economic structures, industrial needs, workforce development strategies, and government policies. In this section, we explore how North America, Europe, and Asia approach PLC training and workforce development.
North America: Emphasis on Certifications and Industry Partnerships
In North America (United States, Canada, and Mexico), the demand for skilled automation professionals is driven by the rapid expansion of smart factories, Industry 4.0 initiatives, and labor shortages in manufacturing. PLC training in this region is characterized by certification-based learning, strong industry partnerships, and a mix of online and in-person training options.
1. Certification-Based Training
- Many automation professionals in North America pursue industry-recognized PLC certifications to enhance their employability.
- Certifications are often offered by automation vendors (Siemens, Rockwell Automation, Schneider Electric) or independent institutions.
- Examples:
- Rockwell Automation's ControlLogix Programmer Certificate
- Siemens S7-1200/S7-1500 Certified Programmer Courses
- ISA Certified Automation Professional (CAP) for broader automation skills
2. Industry Partnerships with OEMs and Universities
- Companies like Rockwell Automation, Siemens, and Omron partner with universities and community colleges to integrate PLC training into engineering programs.
- Examples:
- Purdue University’s SMART Manufacturing program incorporates Allen-Bradley PLC training.
- MIT’s Industrial IoT Lab collaborates with automation vendors for hands-on PLC education.
- McMaster University in Canada provides industrial automation training using Siemens and ABB PLCs.
3. Availability of Diverse Training Options
- Online PLC training programs are widely available through platforms like SolisPLC, Udemy, and Joltek.
- In-person training is common at technical colleges, automation vendors, and industrial training centers.
- Community colleges (e.g., Pennsylvania College of Technology, George Brown College) provide hands-on PLC training integrated with robotics and motion control.
4. Focus on IIoT and Smart Manufacturing
- With Industry 4.0 adoption, PLC training in North America increasingly includes IIoT (Industrial Internet of Things), OPC UA, MQTT, and cloud-based PLC programming.
- Amazon Web Services (AWS) and Microsoft Azure have partnered with industrial automation companies to integrate cloud-based PLC solutions.
Challenges in North America
- Shortage of skilled automation professionals: A 2023 report from the National Association of Manufacturers (NAM) highlights a 2.1 million skilled labor gap by 2030.
- High cost of formal training: Certification programs and university courses can be expensive, making self-paced online training a popular alternative.
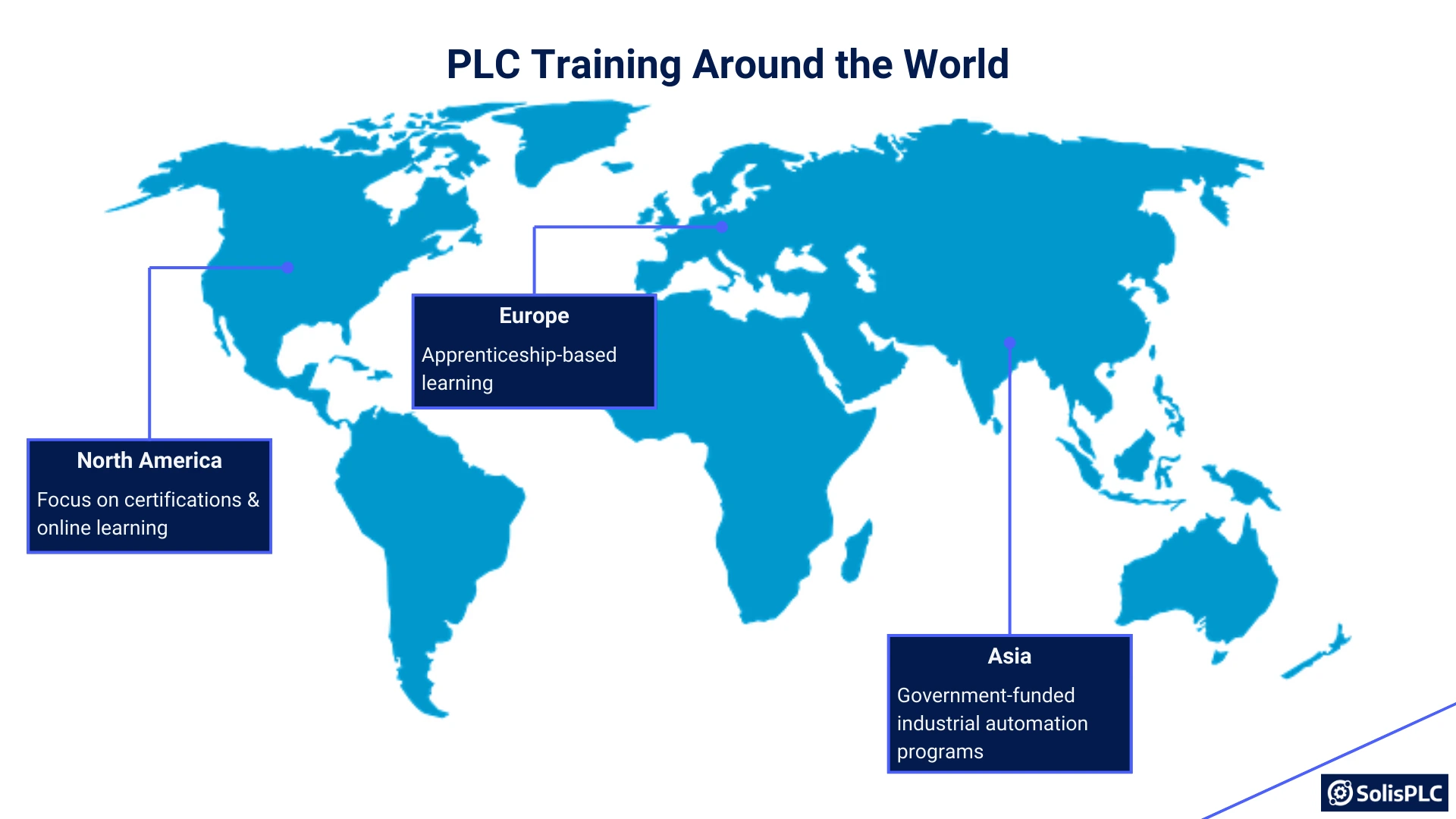
Europe: Strong Focus on Apprenticeships and Vocational Training
Europe has a well-established approach to industrial training, integrating PLC education into engineering and vocational programs. Countries like Germany, the UK, France, and Sweden emphasize hands-on apprenticeships, government-backed automation training, and strong ties between industry and academia.
1. Vocational and Apprenticeship-Based Learning
- Europe follows a dual education model, where students combine classroom learning with real-world apprenticeships.
- Germany’s "Meister" (Master Craftsman) system is a globally recognized approach to PLC and automation training.
- Examples:
- Siemens Technik Akademie (Germany) offers a practical PLC apprenticeship program.
- ABB’s Swiss Apprenticeship Model integrates PLC training with robotics and motion control.
2. Integration of PLC Training in Engineering Curricula
- European universities and polytechnic institutions mandate PLC training as part of electrical engineering, mechatronics, and industrial automation programs.
- Example programs:
- TU Munich (Germany) integrates Siemens TIA Portal and PROFINET into its automation curriculum.
- University of Sheffield (UK) offers advanced PLC coursework with Schneider Electric and Mitsubishi Electric PLCs.
3. Strong Government Support for Automation Training
- The European Union funds digital transformation and automation skills development programs.
- Germany’s Federal Institute for Vocational Education and Training (BIBB) and France’s Industry Future Program actively promote PLC and industrial automation training.
4. Advanced Automation & Industry 4.0 Training
- Europe is a leader in smart manufacturing, and PLC training is evolving to include:
- Cybersecurity for PLC systems (ISO 27001, IEC 62443)
- Cloud-connected PLCs and IIoT applications
- Machine learning and AI in PLC programming
Challenges in Europe
- High demand for multilingual PLC training: With multiple languages spoken across Europe, standardized PLC training material in English, German, and French is needed.
- Cost of PLC hardware: Siemens, ABB, and Beckhoff systems can be expensive, making PLC simulation software more commonly used in training.
Asia: Rapid Adoption of PLC Training to Support Growing Manufacturing Sectors
Asia’s fast-growing manufacturing industries in China, India, Japan, and Southeast Asia are driving demand for skilled PLC professionals. Governments and corporations are investing heavily in technical education, workforce development, and automation integration.
1. Government Initiatives for Industrial Automation Training
- Asian governments recognize the importance of automation education to support manufacturing.
- Initiatives include:
- China’s "Made in China 2025" strategy, which includes large-scale investment in automation and PLC training.
- India’s Skill India initiative, which promotes PLC programming as part of national workforce development.
- Japan’s Industrial AI and Automation Program, which integrates PLC education with robotics and AI.
2. High Demand for PLC Training in Automotive and Electronics Industries
- Asia is the world's largest manufacturer of electronics and automobiles, and PLC training is heavily used in:
- Automotive assembly plants (Toyota, Hyundai, Tata Motors)
- Semiconductor manufacturing (TSMC, Samsung, Intel)
- Pharmaceutical automation (Sun Pharma, Takeda, Biocon)
3. Growing Availability of Online and Technical Institute Training
- India, China, and Southeast Asia have seen rapid growth in online PLC courses and technical training centers.
- Companies like Mitsubishi Electric, Omron, and Delta Electronics provide certified PLC training for engineers.
4. Cost-Effective Training Options & Use of Open-Source PLC Solutions
- Due to cost constraints, many Asian countries use open-source PLC programming tools like Codesys for training.
- Siemens and Mitsubishi Electric provide affordable PLC starter kits for students and technical institutions.
Challenges in Asia
- Standardization of PLC training: Different countries have different educational approaches, leading to inconsistencies.
- Limited access to advanced PLC technologies in smaller manufacturing hubs.
Conclusion
PLC training is a global priority, but its approach differs across regions:
- North America emphasizes certifications, online training, and vendor partnerships.
- Europe focuses on apprenticeships, vocational learning, and government-supported automation education.
- Asia rapidly expands PLC training through government initiatives, industrial demand, and cost-effective training methods.
As automation continues to advance, a standardized, globally recognized approach to PLC education may emerge. The next section will explore challenges in PLC training, including technology evolution, cost barriers, and workforce skill gaps.
Future Trends in PLC Training
As industrial automation continues to evolve, PLC training methods must adapt to meet the needs of modern manufacturing. Traditional classroom-based instruction is giving way to immersive learning experiences, sophisticated simulation tools, and cybersecurity training. These advancements not only improve the effectiveness of PLC education but also prepare professionals for real-world automation challenges.
Incorporation of Virtual Reality (VR) and Augmented Reality (AR) for Immersive Learning
Enhancing Hands-On Training with VR and AR
Virtual Reality (VR) and Augmented Reality (AR) are transforming PLC training by offering immersive, hands-on experiences without the need for physical hardware. These technologies allow learners to interact with virtual PLC systems, control panels, and factory environments, making training more engaging and effective.
Key Benefits of VR/AR in PLC Training
- Risk-Free Environment – Trainees can experiment with complex control logic, troubleshooting, and industrial safety protocols without the risk of damaging real equipment.
- Enhanced Accessibility – Engineers and technicians in remote locations can access high-quality training without requiring travel to a physical training center.
- Real-Time Guidance – AR applications can overlay real-time PLC schematics, wiring diagrams, and troubleshooting steps onto a real machine, assisting technicians on-site.
Examples of VR/AR in PLC Training
- Siemens has integrated VR into its PLC training programs, allowing engineers to virtually navigate factory automation systems and interact with PLC components.
- Rockwell Automation’s AR-powered FactoryTalk Innovation Suite provides real-time visualization of control systems, helping technicians troubleshoot PLC logic without opening control cabinets.
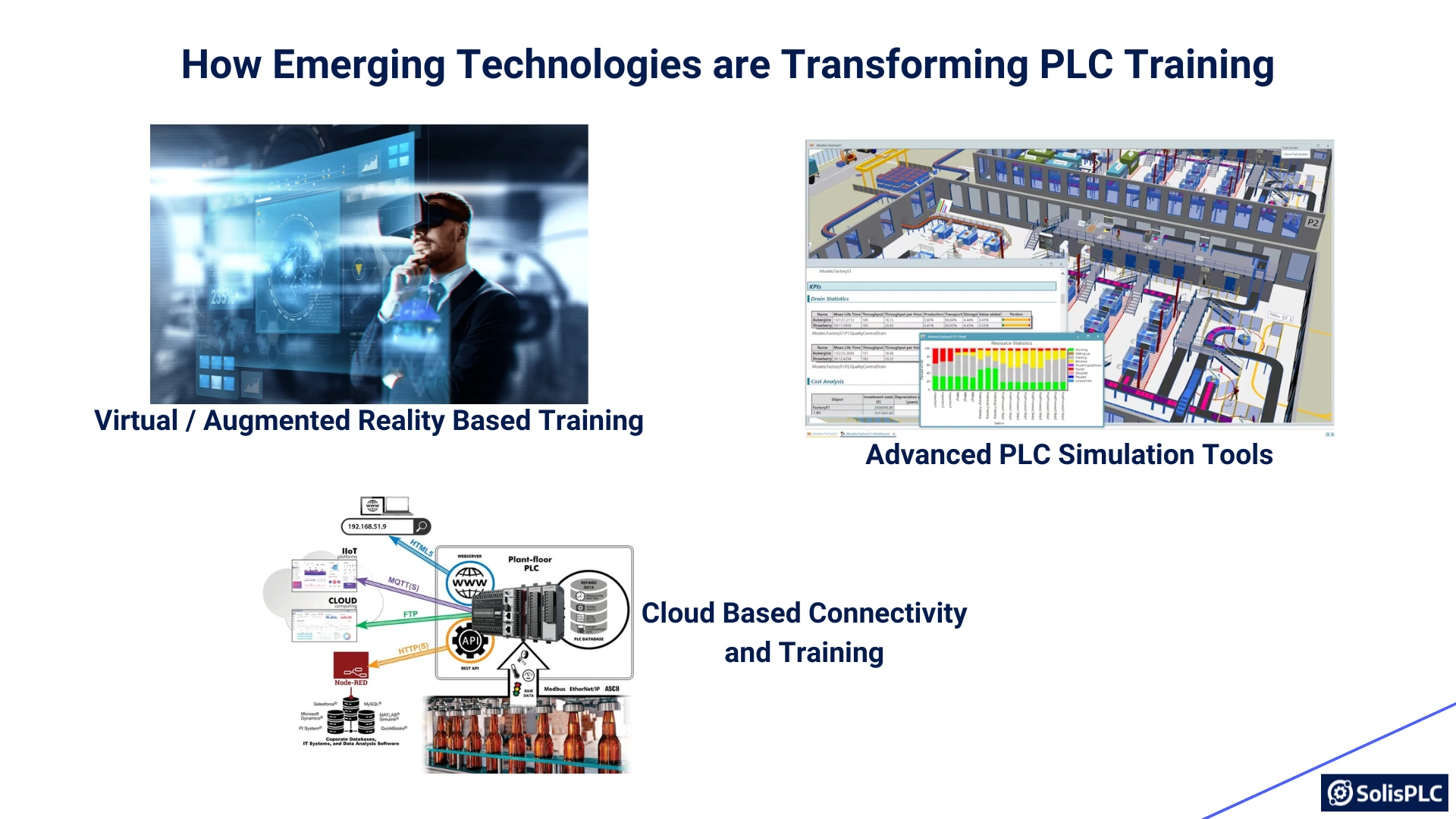
Development of Advanced Simulation Tools for Realistic Practice Scenarios
Evolution of PLC Simulators
Simulation tools have become a critical component of modern PLC training, allowing learners to develop and test automation programs without requiring physical PLCs. These tools mimic real-world industrial scenarios, enabling engineers to simulate production lines, troubleshoot faults, and optimize control logic.
Benefits of Advanced Simulation in PLC Training
- Cost Savings – Eliminates the need for expensive PLC hardware, sensors, and actuators during training.
- Realistic Testing Environment – Provides a controlled space to test ladder logic, structured text, and function block diagrams before deploying programs to actual machines.
- Industry-Specific Simulations – Allows training in sector-specific automation, such as automotive assembly lines, packaging systems, and process control plants.
Leading PLC Simulation Tools
- Siemens TIA Portal PLCSIM Advanced – Offers high-fidelity virtual PLC programming and interaction with digital twins of industrial processes.
- Allen-Bradley Studio 5000 Logix Emulate – Enables engineers to test and debug ControlLogix and CompactLogix programs before deploying them to live systems.
- Factory I/O – A real-time industrial automation simulator that integrates with Siemens, Allen-Bradley, and Codesys PLCs, allowing trainees to build and test production lines in a 3D environment.
Growing Importance of Cybersecurity Training within PLC Curricula
Cybersecurity Risks in Industrial Automation
With the increasing adoption of Industry 4.0, cloud connectivity, and IIoT (Industrial Internet of Things), industrial control systems are becoming prime targets for cyber threats. PLCs, once isolated, are now connected to networks, databases, and cloud platforms, making them vulnerable to hacking, malware, and unauthorized access.
Key Areas of Cybersecurity in PLC Training
- Secure PLC Programming Practices – Emphasizing password protection, access control, and secure ladder logic development.
- Industrial Network Security – Training on firewalls, VLAN segmentation, and secure communication protocols such as OPC UA, MQTT with TLS, and PROFINET with security enhancements.
- Incident Response and Threat Mitigation – Educating automation professionals on detecting, analyzing, and responding to cyberattacks on industrial networks.
Cybersecurity Training Programs for PLC Engineers
- Siemens Industrial Security Training – Covers best practices for securing PLCs, HMIs, and SCADA systems.
- Rockwell Automation’s Cybersecurity Certification – Focuses on protecting industrial networks and implementing secure automation frameworks.
- ISA/IEC 62443 Certification – A globally recognized industrial cybersecurity standard that is becoming essential for PLC programmers and control engineers.
Conclusion
The future of PLC training is highly dynamic and technology-driven. VR/AR, advanced simulation tools, and cybersecurity education are revolutionizing how engineers and technicians learn, practice, and implement industrial automation solutions.
As manufacturing continues to integrate Industry 4.0 technologies, modern PLC training must evolve to include immersive learning, realistic practice environments, and cybersecurity expertise. The next generation of automation professionals will need not just programming skills, but also the ability to work in digital twin environments, defend industrial networks, and adapt to rapidly changing control technologies.
Conclusion: The Ongoing Importance of PLC Training
PLC training is more than just a technical skill—it is an essential investment for professionals and industries striving to increase automation efficiency, reduce downtime, and stay competitive in modern manufacturing. As factories become smarter and more interconnected, the demand for skilled PLC programmers, automation engineers, and maintenance technicians continues to grow.
Recap: The Critical Role of PLC Training in Industrial Automation
Throughout this guide, we explored why PLC training is essential and how it impacts manufacturing, engineering, and industrial processes. Key takeaways include:
- Automation and Efficiency – Skilled PLC professionals optimize production, troubleshoot faster, and minimize operational disruptions.
- Industry Demand – As industries move toward Industry 4.0 and IIoT, companies actively seek engineers and technicians with PLC expertise.
- Diverse Learning Paths – Training is available through online courses, in-person workshops, and vendor certifications, catering to different learning styles and experience levels.
- Technological Advancements – Virtual reality, advanced simulation tools, and cybersecurity training are reshaping the future of PLC education.
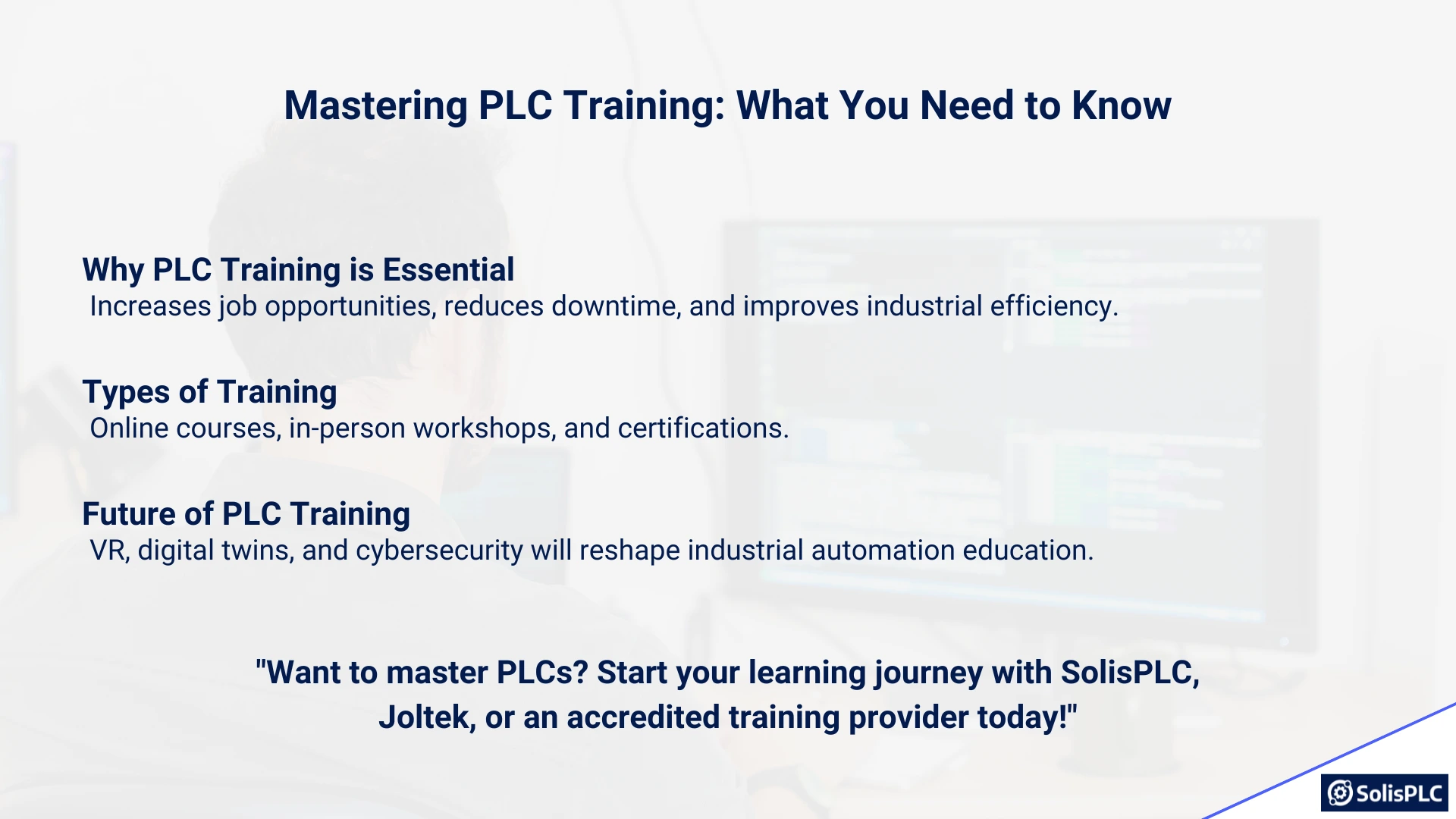
Encouragement for Continuous Learning
Industrial automation never stops evolving, and neither should your training. The best engineers and technicians continuously expand their knowledge, staying up to date with:
✅ New PLC technologies – Understanding advancements in cloud-based PLC programming, edge computing, and AI integration.
✅ Cybersecurity best practices – Protecting industrial networks from cyber threats as PLCs become more connected.
✅ Cross-platform expertise – Learning multiple PLC environments (Allen-Bradley, Siemens, Mitsubishi, Schneider Electric) to enhance job opportunities.
✅ Hands-on troubleshooting skills – Practicing real-world PLC fault diagnostics to become a highly valuable asset in any manufacturing environment.
Call to Action: Take the Next Step in Your PLC Training Journey
🚀 Whether you’re a beginner looking to start your PLC journey or an experienced professional aiming to upskill, the right training can open new career opportunities and improve industrial operations.
🔹 Get started with online PLC training from SolisPLC or Joltek
🔹 Consider a vendor-certified course from Siemens, Rockwell Automation, or Mitsubishi
🔹 Join automation communities and forums to keep learning
💡 The future of industrial automation depends on skilled professionals—make sure you're one of them!