IIoT Applications
IntroductionÂ
Industrial IoT applications are revolutionary, transforming traditional industries and creating new opportunities. They're used in various industrial settings, from manufacturing to mining, agriculture to energy management, healthcare to transportation. They are the driving force behind Industry 4.0, a term that describes the next level of automation and data exchange in the manufacturing sector.
This tutorial will provide an insightful overview of IIoT applications, delving into their diverse and impactful implementations across various industries.Â
IIoT Applications
Smart robotics
Industrial robots are one of the prominent components in the factory; due to their flexibility and automized operation, they are widely used in the organization. What if industrial robots communicate with each other in the cloud? It is possible by integrating IoT with industrial robots.
Power and robotics firm ABB is one of the most visible to embrace the concept of predictive maintenance, using connected sensors to monitor its robots’ maintenance needs and trigger repair before parts break. Also related to IoT is the company’s collaborative robotics. Its YuMi model, which was designed to collaborate alongside humans, can accept input via Ethernet and industrial protocols like Profibus and DeviceNet. ABB robots offer some applications like:
- Paint Process Automation
- Integrated Dispensing Function Package
- Machining Cell
- Material Handling
- Packaging and palletizing
- Welding
- Vision systems
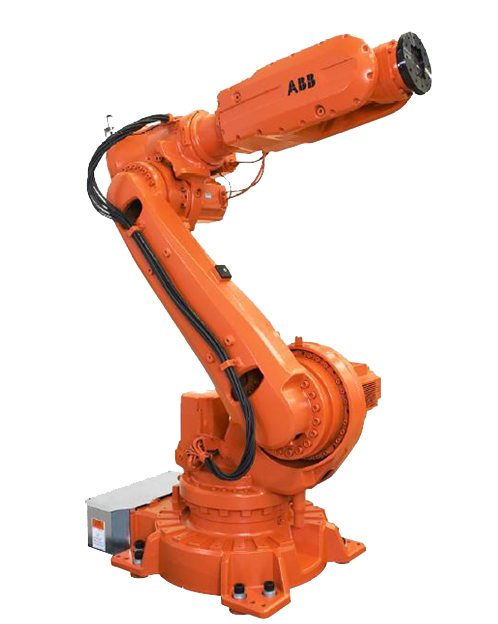
Also ABB used Integrated Force Control sensors that Measures all six components of force and torque to allow robots to operate with the dexterity of the human hand.
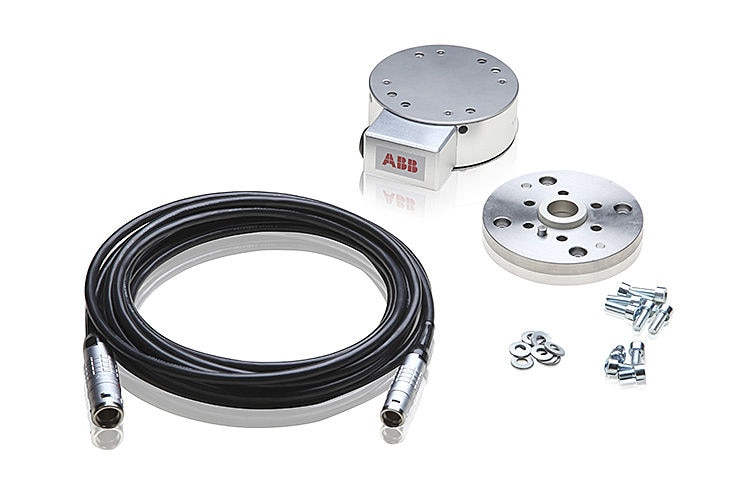
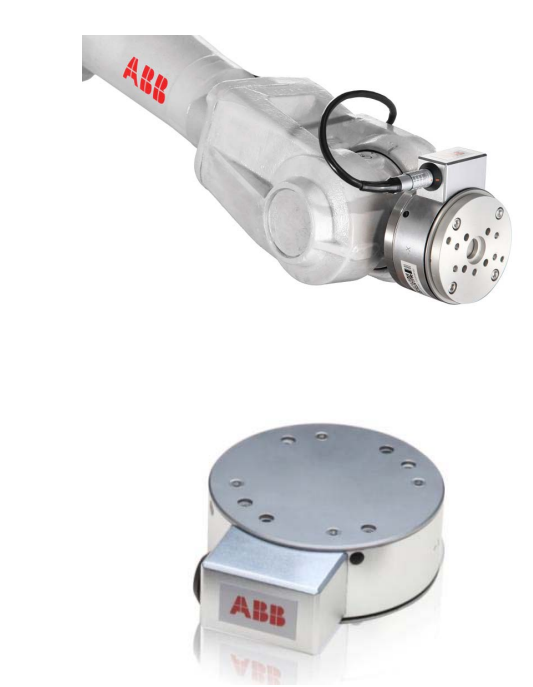
To program ABB robots, we can use:
- RobotStudio: ABB's simulation and offline programming software, RobotStudio, allows robot programming to be done on a PC in the office without shutting down production; this allows you to perform tasks such as training, programming, and optimization.
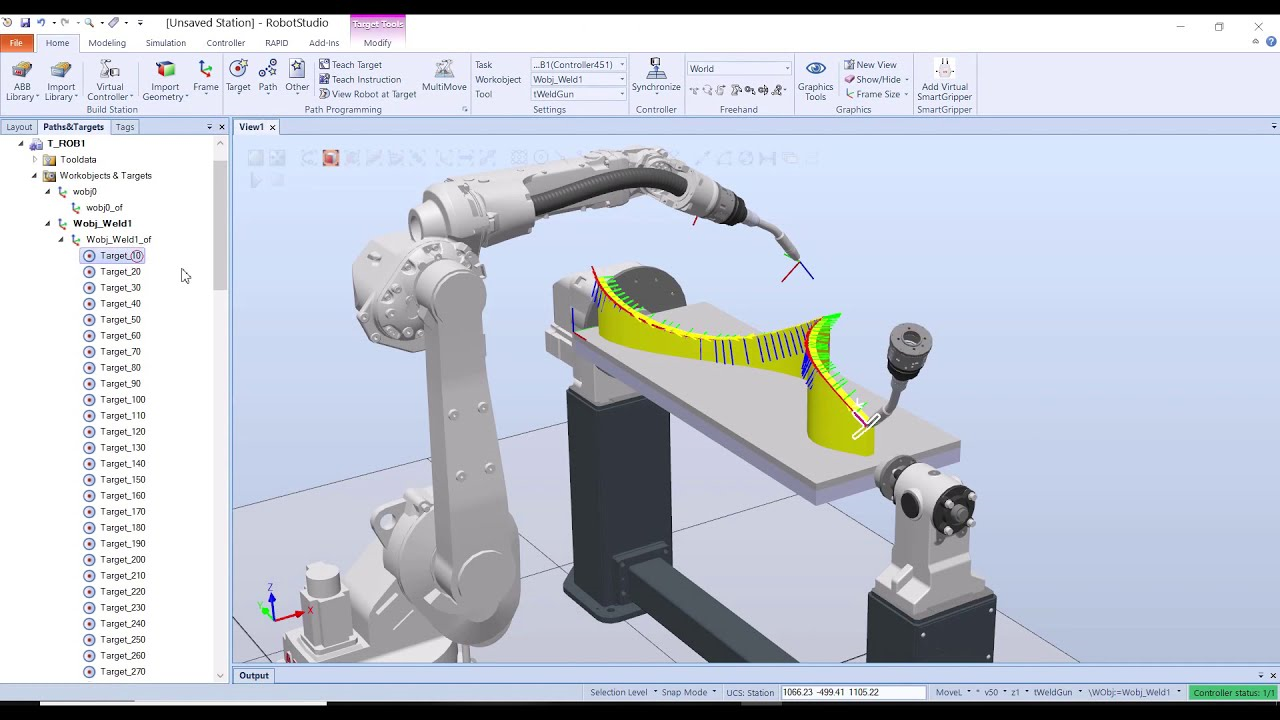
- RoboDK: RoboDK is an offline programming and simulation software that works with a wide variety of robot brands. It is compatible with many ABB models, which you can find in the online Robot Library. As an offline programming tool, you can program your robot with RoboDK without taking the robot out of production. No programming skills are required with the intuitive RoboDK graphical interface. Overall, you can even use the RoboDK API to program robots in your favorite programming language.
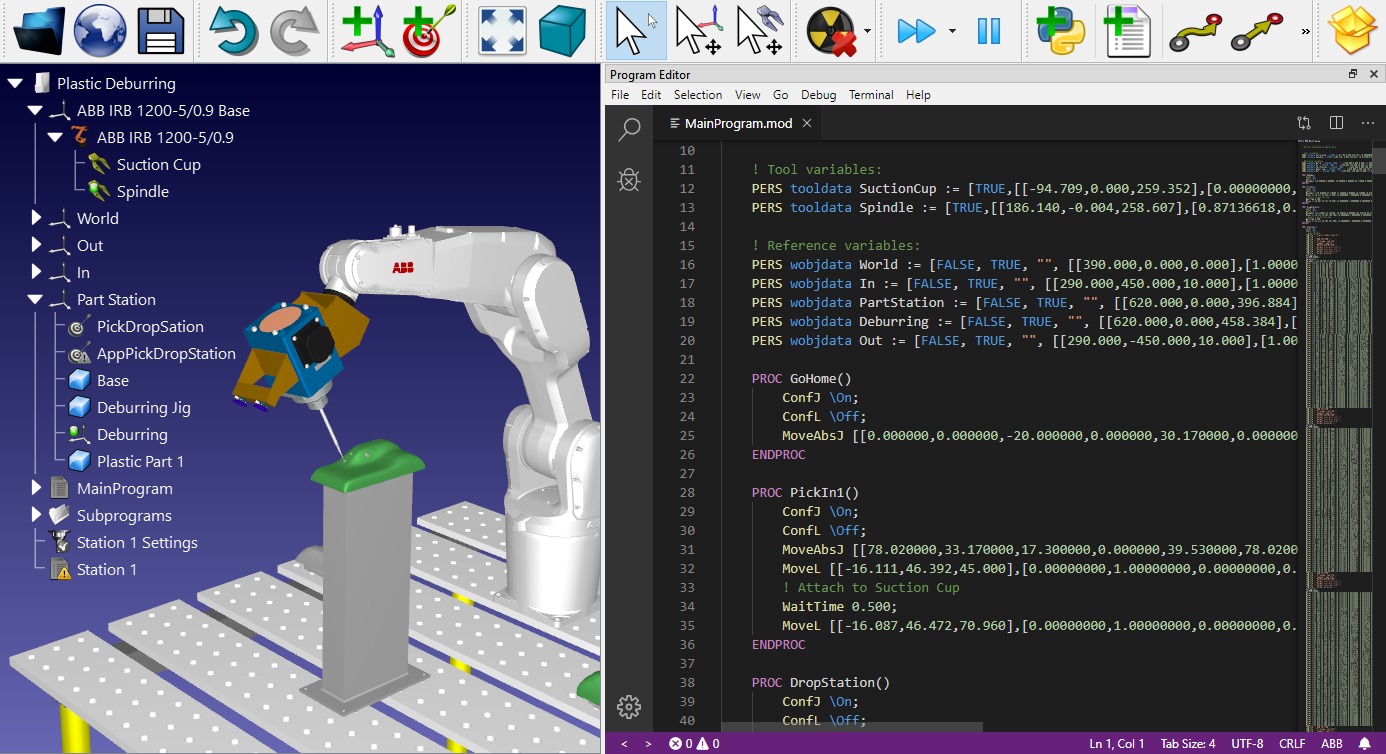
Let’s now get into more details and see how to implement IIoT in robot industry. There is research done by “KTH Royal Institute of Technology” to promote uniform connectivity across a company and to improve production performance by reducing unwanted stops. It is focused on two robots from different manufacturers; one of the robot variants was YR-1-06VXH25 from Yaskawa, and the other robot was IRB 2600 from ABB with a defined robot controller IRC 5 for ABB including MyABB interface and PEMA for Yaskawa robots.
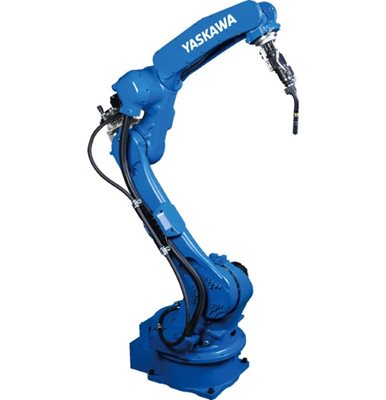
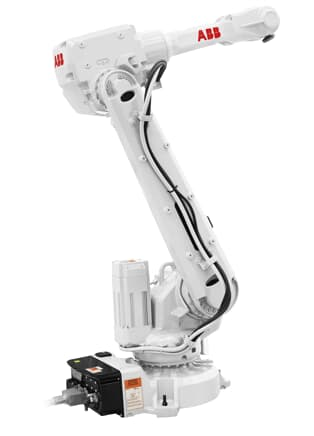
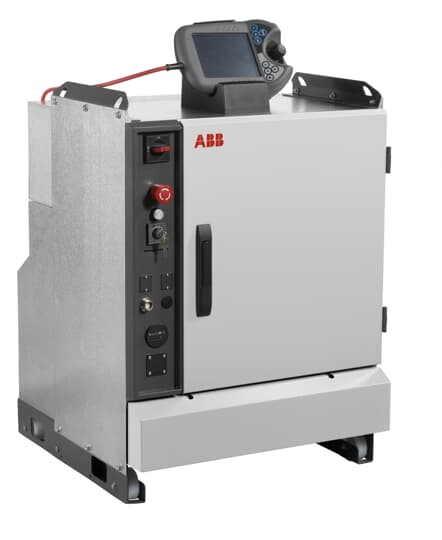
The research further investigated the current user interface used by VCE (Volvo construction equipment). The interface software that monitors the robots is GEMA, which is a running state monitor software that manages to visualize the robots' current processing state, such as programming, running, and stop status. Apart from visualizing the running state, the defined software does not monitor or provide any real-time tracking of the system. IIoT technology will be used to concentrate on the issues and problems that lead to unplanned stops.
Let’s briefly explain the step-by-step process involved in designing the required dashboard and alert system from the initial step using ThingWorx IIoT software.
- Data binding: this process helps connect the database and the user. Different machines VCE uses a common integrated KepServerEx which enables the user to connect, manage, and monitor various equipment and software through a single server.
- KepServerEx: connecting and managing the data from all the devices in the factory; this server enables the company to facilitate a single server entity and makes the process more efficient and reliable. The two selected robots were bound and connected to the Kepware platform. And as we know, KepServerEx uses an OPC-UA communication protocol for tunneling the data according to the organization’s needs, and connecting the required data tags to the OPC server which enhances data connectivity between the systems. The connected tags were later retrieved into the IIoT platform for further testing and analysis.
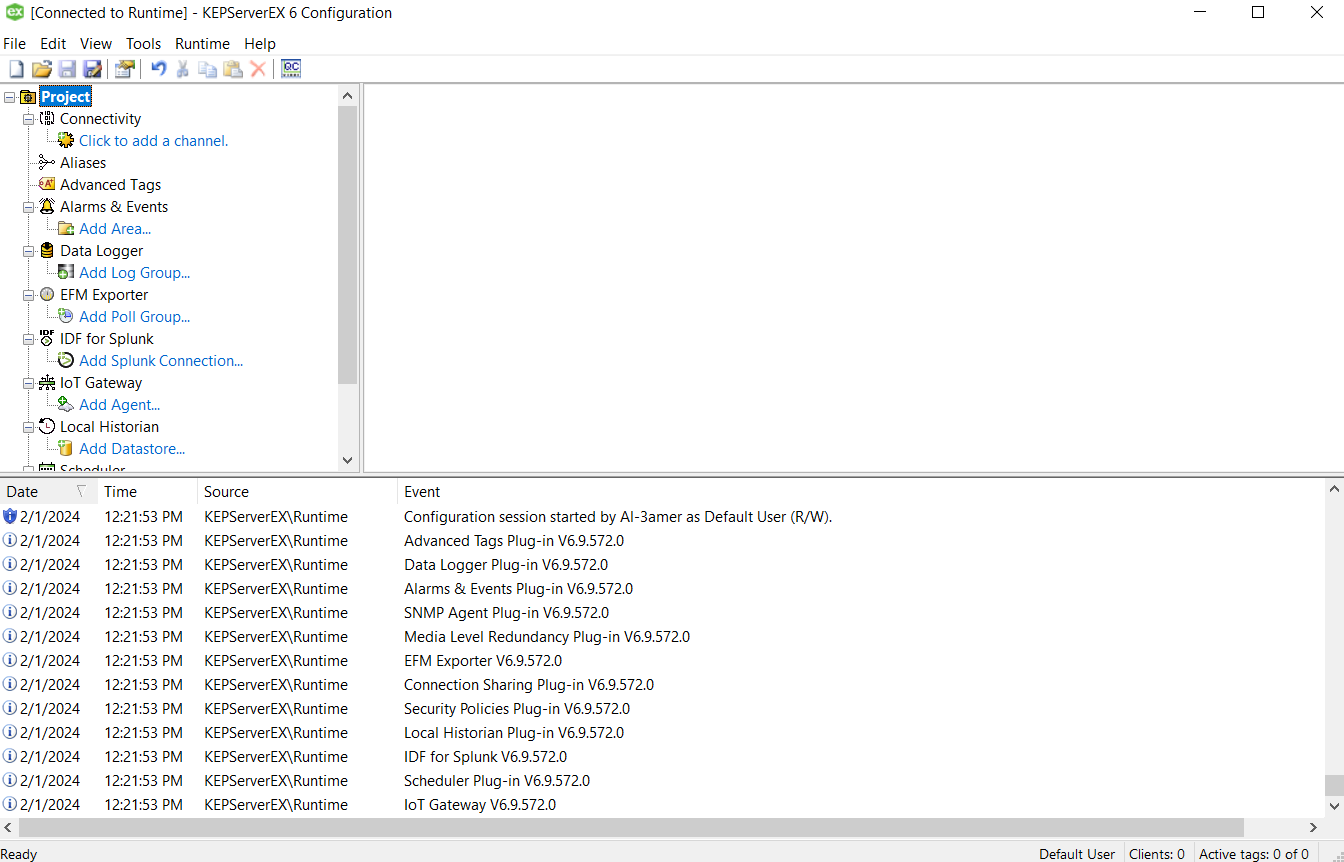
- OPC UA: OPC helps in the communication between the client and the server, based on the software architecture in VCE the required robots were initially connected to the industry’s test server (the company uses two servers, one server for the testing environment and the other one for the production environment). After binding the required robots to the test environment to ensure seamless connectivity and accessibility, the data tags from the test server were replicated and aggregated to the OPC in real time.Â
- Connection between OPC and ThingWorx: send robot’s data to ThingWorx platform over OPC UA.
- Dashboard Development: The formulated data and information are further used in the visualization process, PTC ThingWorx uses a predefine in built mashup interface for enhancing data representation and visibility, ThingWorx data table is an entity which stores, retrieves, and analyzes the data within the IoT platform.
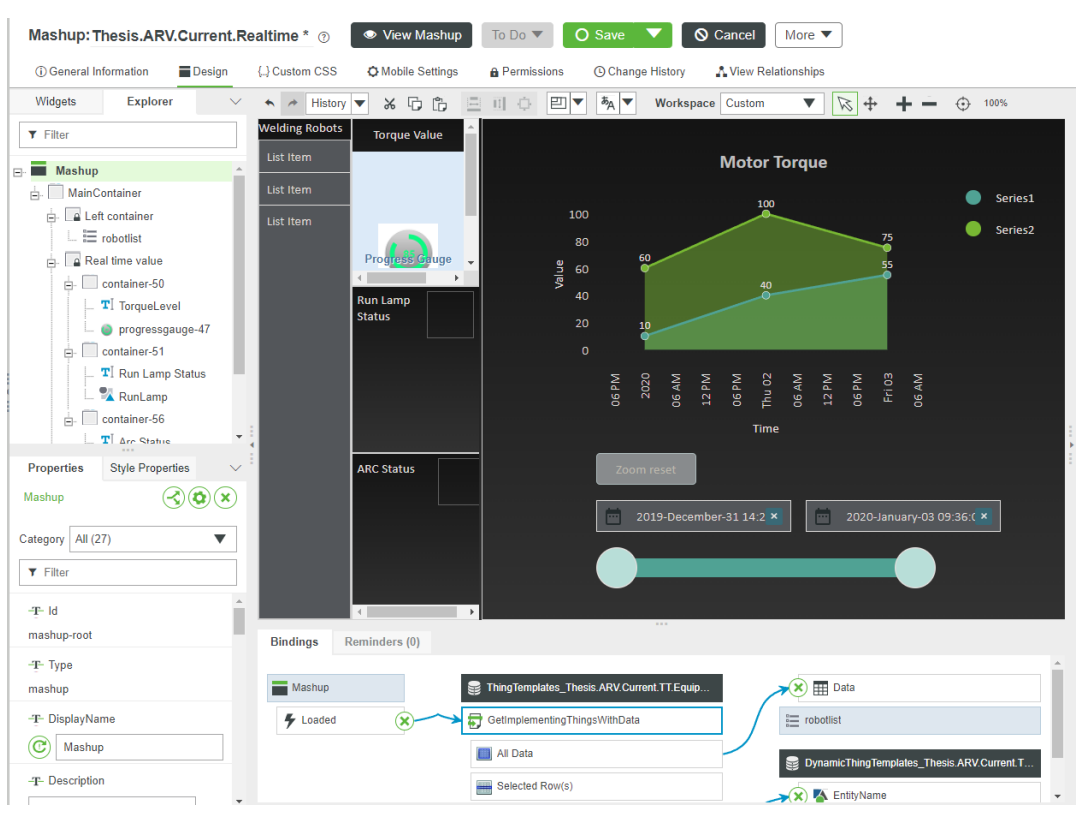
- Development of Alert feature: create notification service that sends the alert through SMS and Email, based on the needs, either one or both modes can be opted for acquiring the service.
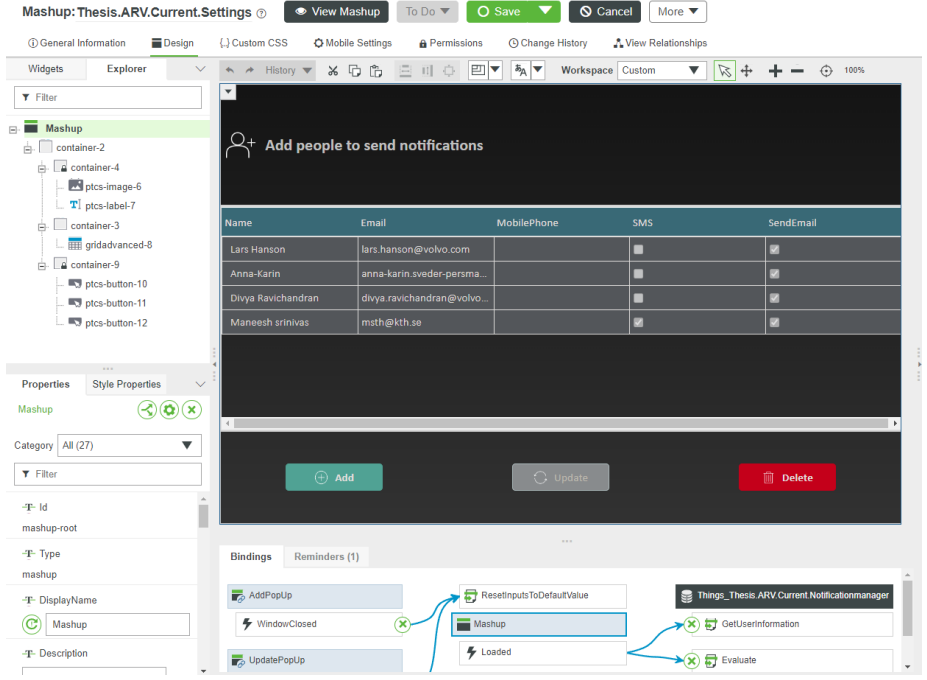
This is the final dashboard and alert system interface
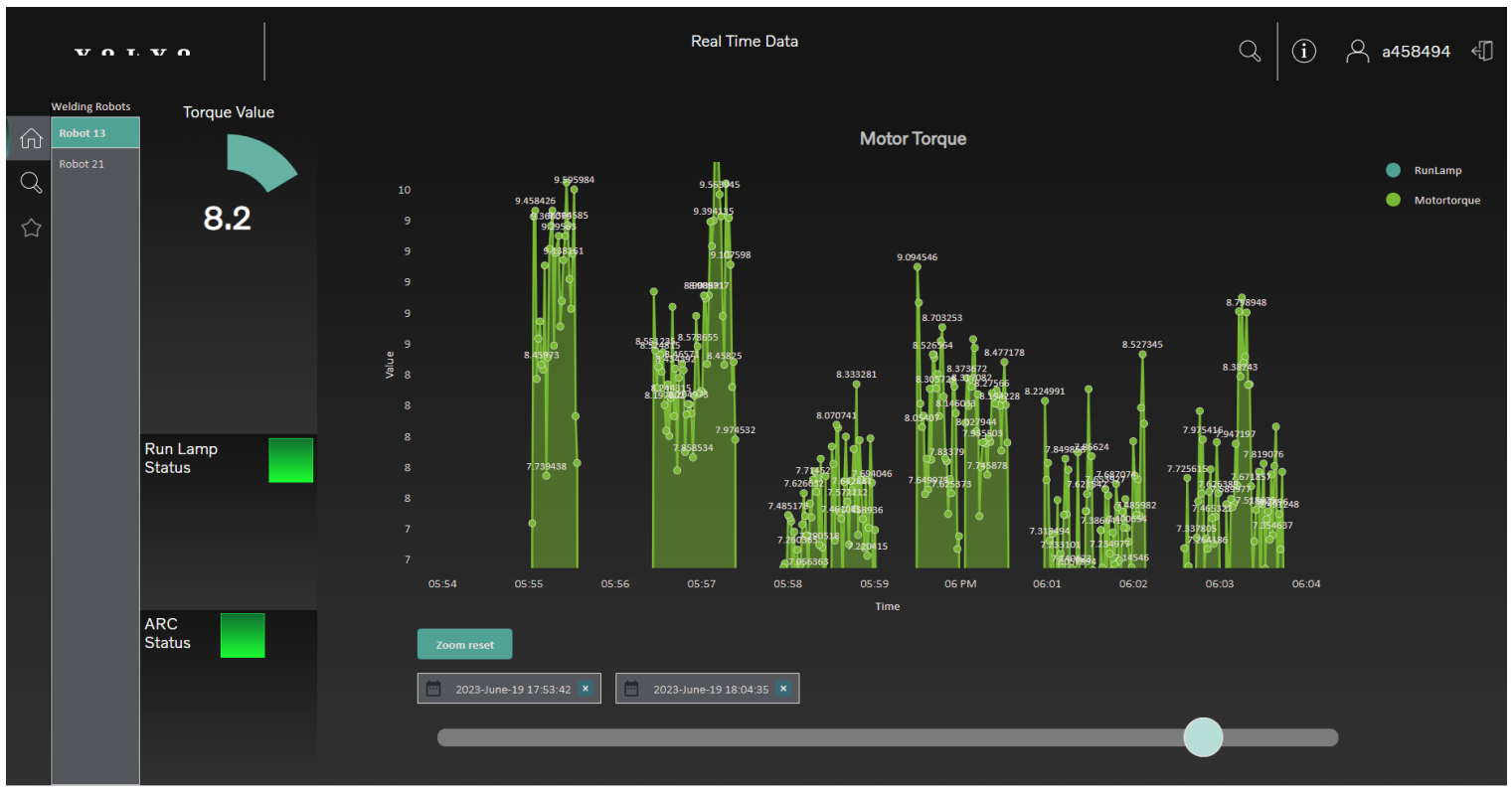
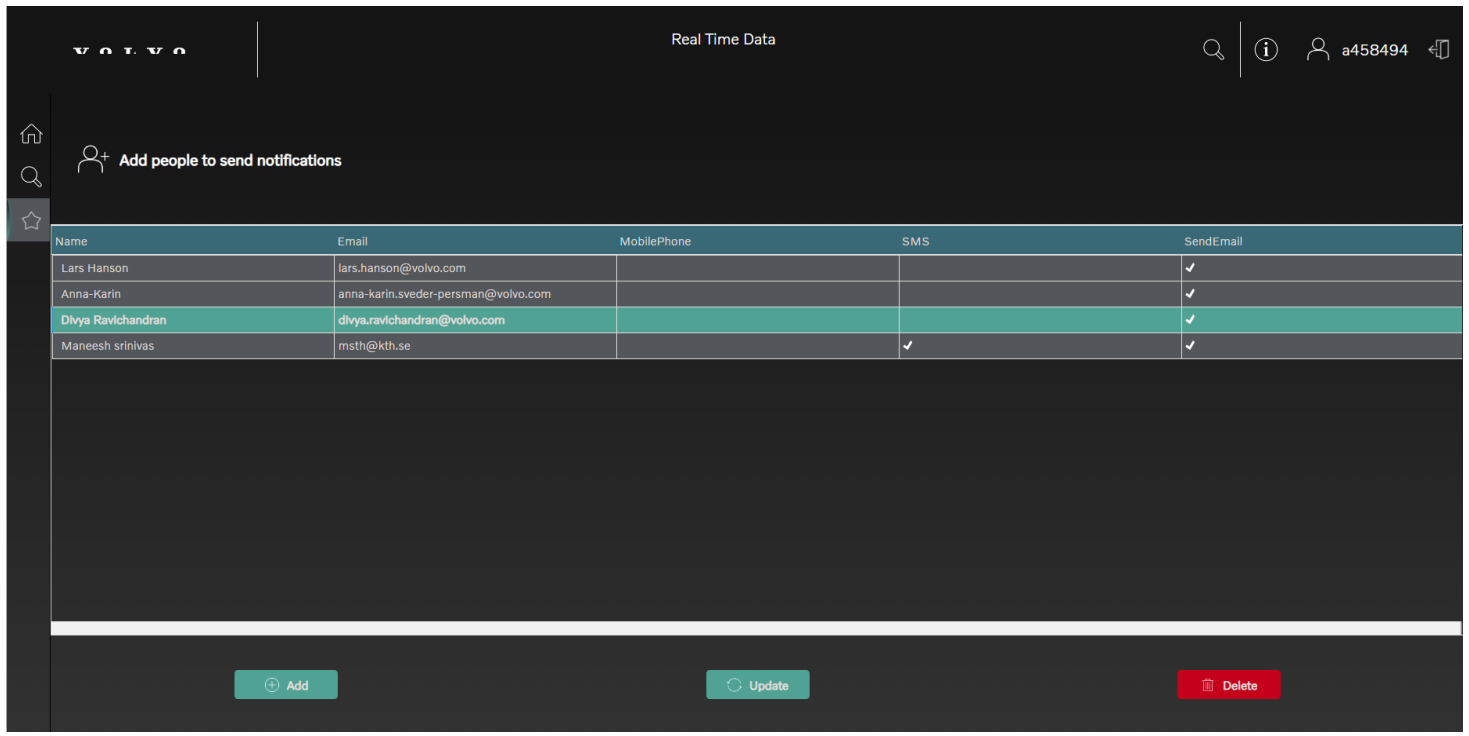
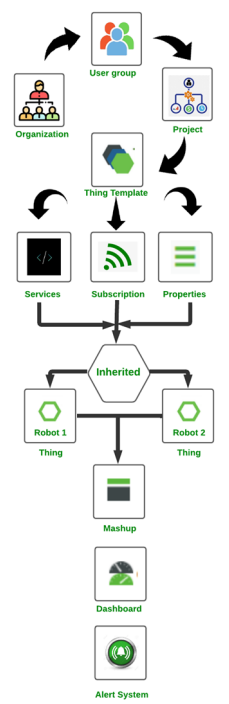
Now, after getting data and making a dashboard and Alert System using IIoT platform, analysis data and through alert notification system’s problems can resolve fast and system can be improved
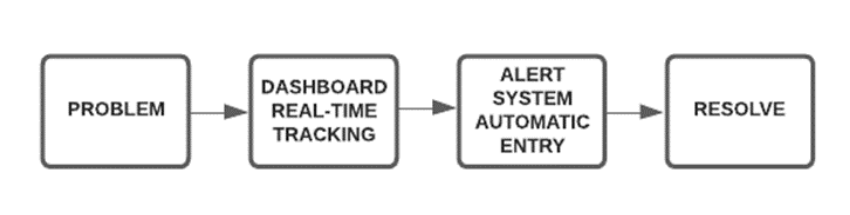
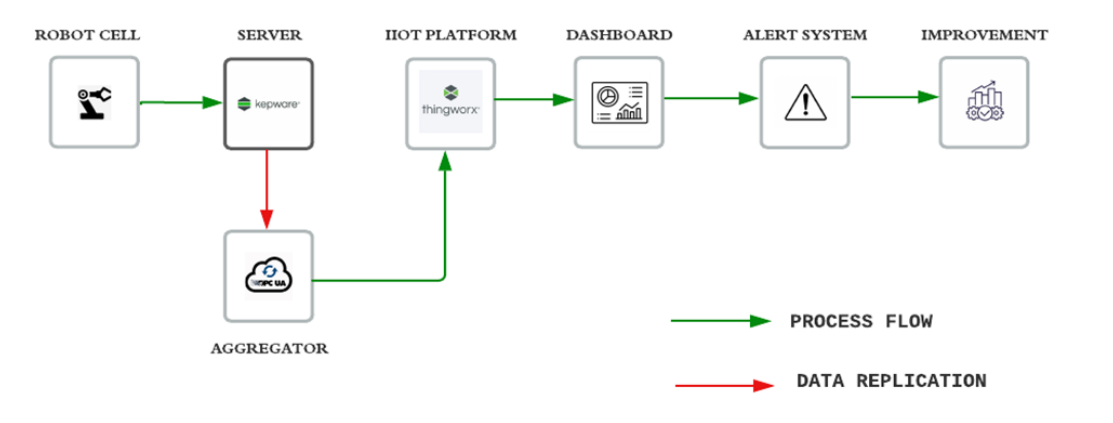
Another example is FANUC's robotics, FANUC's Industrial IoT strategy involves using sensors, data analytics, and cloud computing technologies to collect, process, and analyze data from robotic systems and other manufacturing equipment. This data can then be used to optimize production processes, identify potential issues before they become problems, and improve overall equipment effectiveness; one of its important benefits is the ability to perform predictive maintenance on their robotic systems and other manufacturing equipment. By monitoring equipment performance in real-time and analyzing sensor data, FANUC can identify potential issues and schedule maintenance before equipment failure occurs. This technological advantage reduces downtime, improves equipment reliability, and extends the lifespan of manufacturing equipment.
By leveraging the power of the IoT, FANUC is helping to transform the manufacturing industry and improve efficiency, quality, and safety in production processes.
One of Fanuc’s IIoT Solutions is:
- The FANUC Intelligent Edge Link and Drive (FIELD) system: FIELD system offers customers an open platform that collects machine data and monitors the operating status of their manufacturing equipment in real-time.
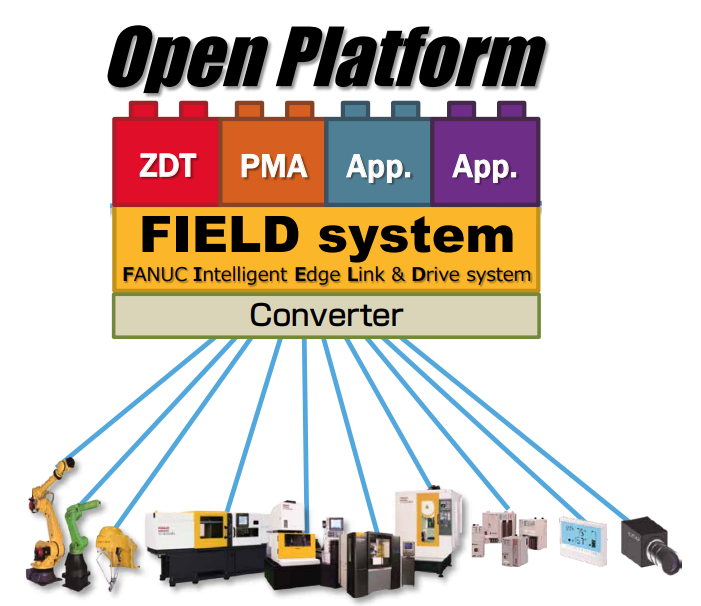
Some of its functions:
- Connection not only to the latest Fanuc products but also to existing machinery in the factory.
- General communication standard as OPC UA and MTConnect.
- Production device manufactures can create and provide converters for their production devices.
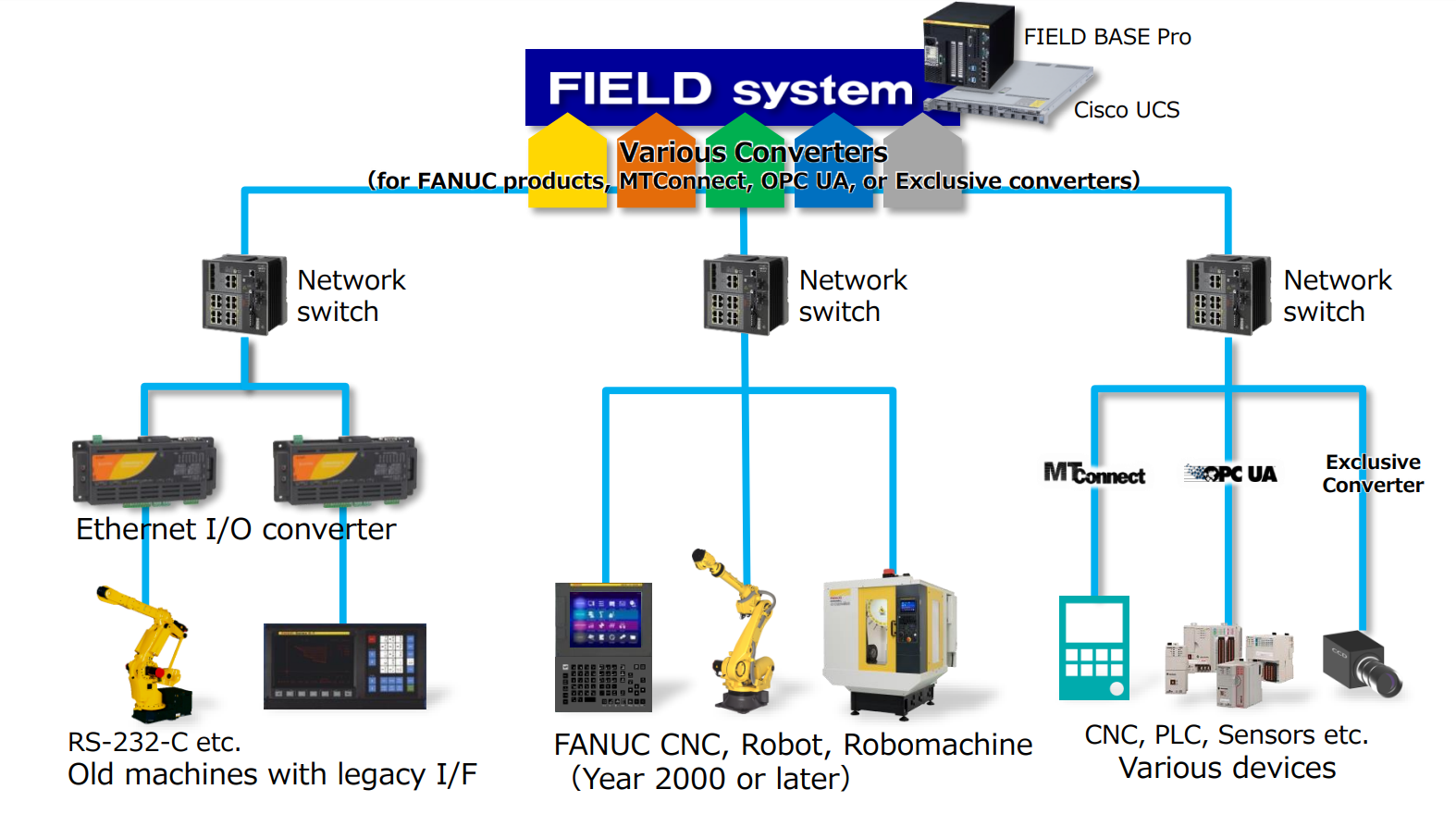
Number of devices can connected to FIELD BASE Pro is Around 30 units
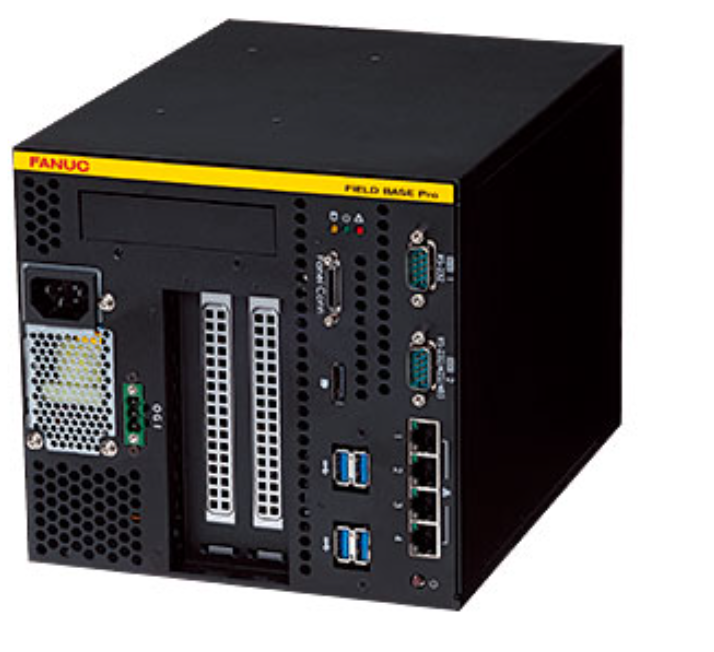
And Number of devices can connected to Cisco UCS C220 is Around 150 units
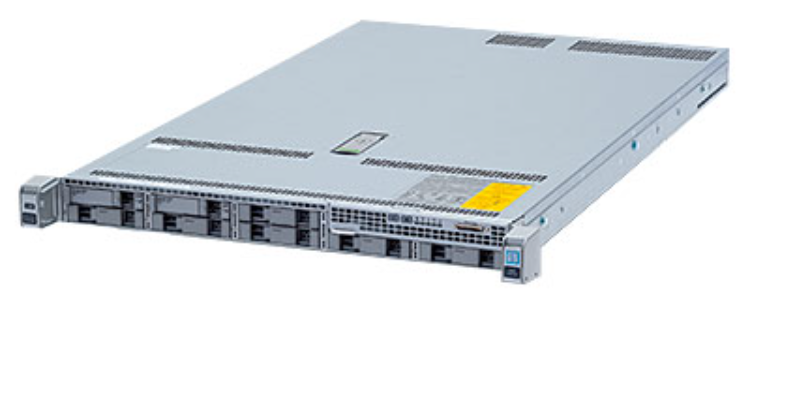
 Now let’s talk briefly about ZDT and PMA:
- FIELD system PMA: FIELD system PMA is an application to analyze factory operation and improve productivity by monitoring the operating status of each production device in real-time, and collecting the operation results of each production device, including the operating time and alarm time and using them for factor analysis.
FIELD system PMA is helpful in improving productivity by statistically analyzing collected data and visualizing tendencies and statuses with numerical values and graphs.
- FIELD system ZDT: FIELD system ZDT is an application to reduce unexpected downtime of production devices. It monitors the statuses of FANUC CNCs and robots and generates error alerts, notifies the user of periodical maintenance and encourages preventive maintenance, and reduces maintenance costs and the workload of maintenance staff by centrally managing the maintenance statuses of production devices. There are two types of ZDT :
- ZDT on Robot-Link (on premise).
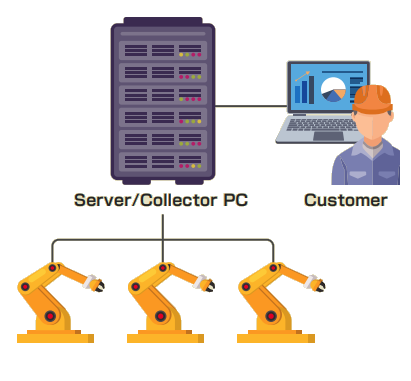
Â
- ZDT on Robot-Link (Cloud).
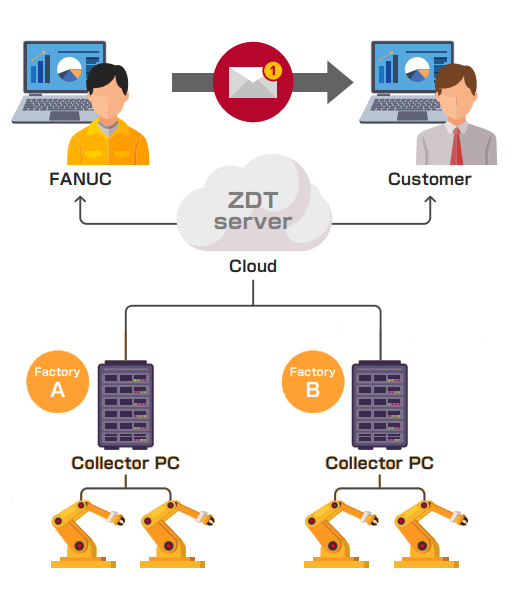
Â
Note | Data can be centralized by server, and also can be monitored by smartphones.
Now let’s see another Application
Asset tracking
Asset tracking is all about knowing where assets (equipment and vehicles) are located at relevant times or moments of time when they move or experience detectable events.
One of the IIoT applications is that it can automate asset finding and monitoring. Companies can outfit their assets, such as finished goods, raw materials, tools, and packages, with radio frequency identification (RFID) tags. These tags are scanned with RFID readers to display information on the corresponding item. Another option is to use equipment sensors that transmit signals over Bluetooth.
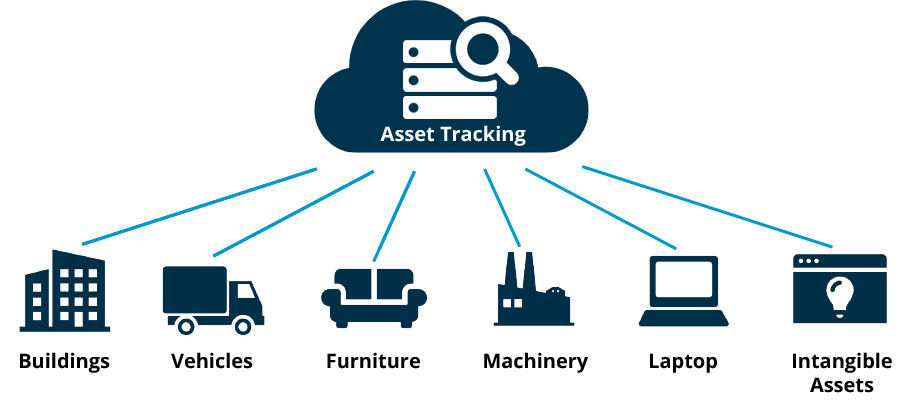
As example:
Bosch Track and Trace:
Bosch has developed a smart tracking solution called Track and Trace that focuses on the needs of load carrier managers and planners, providing them with up to date information on the position and status of any loading equipment.
Custom dashboards ensure that each user group can access exactly the information that it requires.Â
To enable asset tracking in real time, sensors are permanently attached to the load carriers. Logistics specialists receive regular updates regarding the location of the equipment and, if necessary, the status of the goods. Routes can be tracked in real time, thus enabling immediate identification of disruptions or delays.
And IoT gateways collect the sensor data and enrich it with position data before transferring it to the application in the cloud. Gateways are easily attached and can withstand even the harshest conditions. The localization is usually based on GPS, while the transfer takes place via GSM.
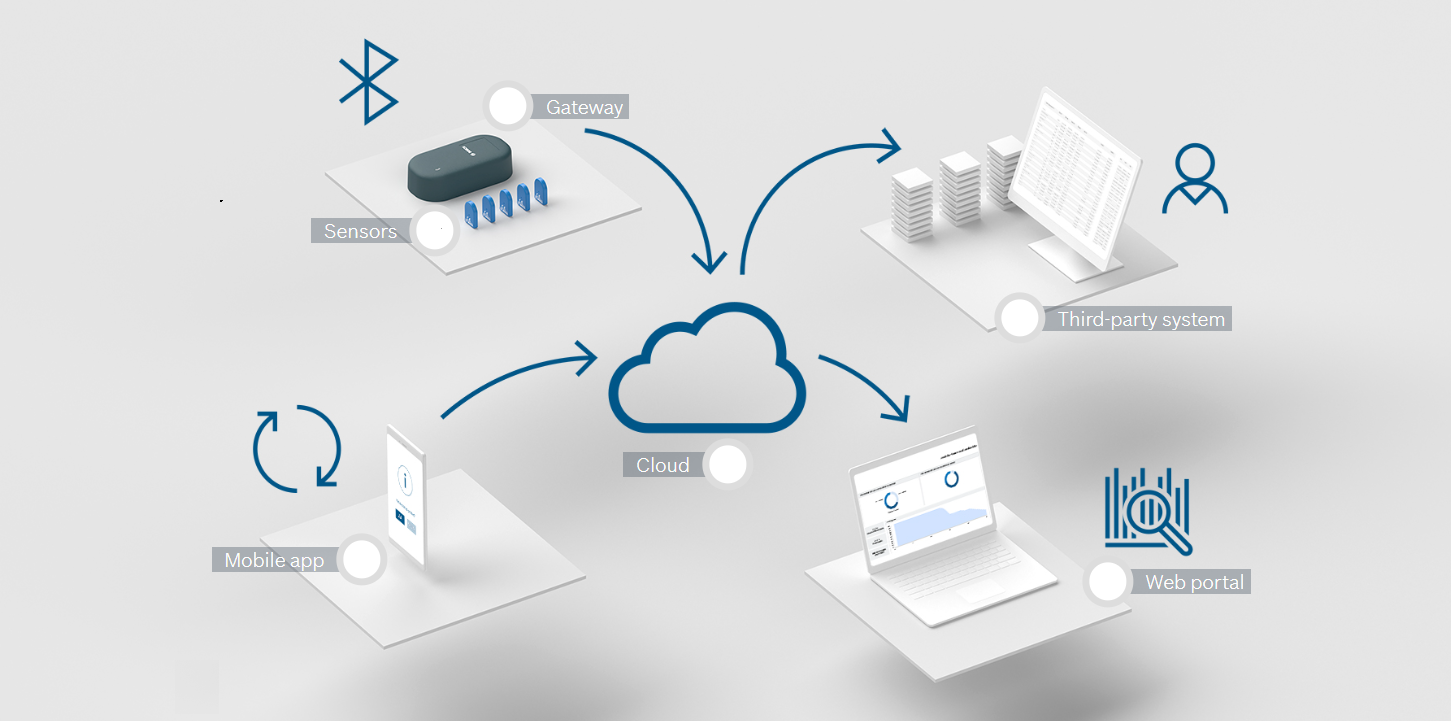
The Track and Trace system brings valuable benefits for the company, resulting in:
- Up to 25% higher utilization of load carriers: no new investments required.
- Up to 75% less searching, inventory, posting, and scanning work.
- Up to 50% time saving for status updates and coordination.
- More Than 50% reduction in lost load carriers.
Quality control
IIoT allows manufacturers to monitor their products at any stage, starting with raw materials, and all the way as the item moves along the production line. This even includes the amount of waste emitted during the manufacturing process and all in real time visualization, this can greatly improve quality control.

Coca-Cola is an example of a company that has used IoT for quality control. Coca-Cola placed sensors on its production line that monitored the quality of its products in real time.
The sensors collected data on temperature, pressure, and other parameters, which were then analyzed using machine learning algorithms.
As a result, Coca-Cola was able to detect anomalies in real time and address them before they become bigger problems, reducing the risk of producing defective products and improving the customer experience.
Autonomous vehicles
Automotive industries are using IoT to enable self driving vehicles to supply goods and logistics management within their company premises. Smart vehicles can detect traffic congestion along its path and make deviations to reach its destination in the shortest time. These vehicles are equipped with many smart sensors continuously detect location data using GPS and wireless technologies for communication with the control station.
Current Trends and Applications of IIoT in Cars:
- Enhanced Vehicle Safety: One of the most significant benefits of IoT in the car industry is improved safety. Vehicles are equipped with a range of sensors that collect real time data, allowing for proactive safety measures.
- Predictive Analytics: enables car manufacturers and service providers to monitor the health of vehicles remotely, leading to improved maintenance practices.
- Personalized Driving Experience: allows for personalized and seamless driving experiences. By integrating smart devices and applications, drivers can enjoy enhanced convenience and connectivity.
- Traffic Management and Optimization: By collecting and analyzing data from multiple vehicles and infrastructure, traffic patterns can be monitored and managed effectively.
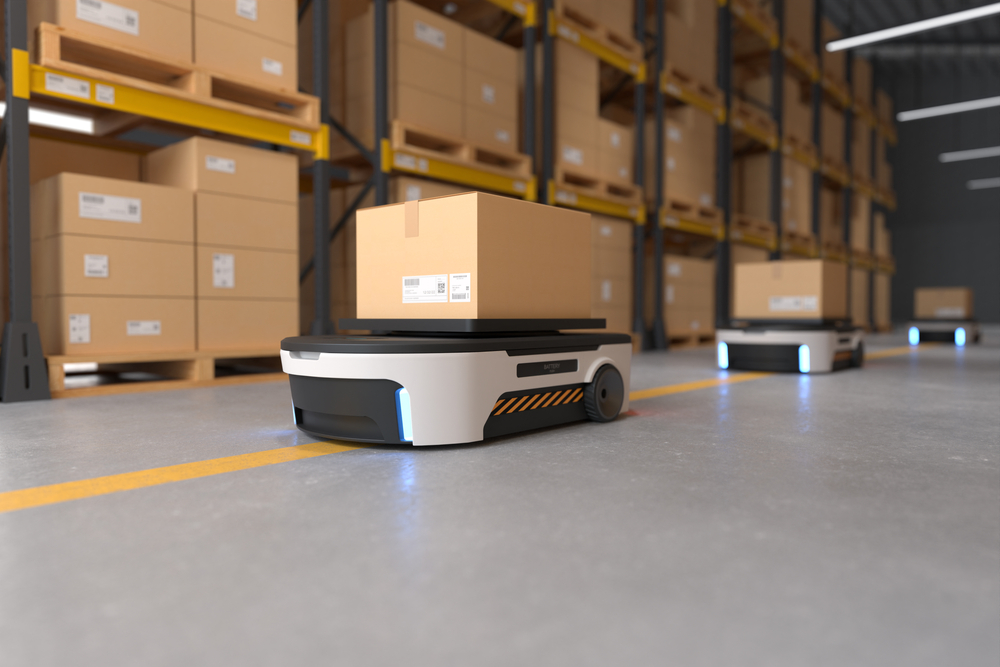
One of Future Implications of IOT in the Car Industry is Vehicle to Vehicle (V2V) Communication: enables vehicles to communicate with each other in real time, forming a network. This allows cars to share important information, such as road conditions, traffic flow, and potential hazards. V2V communication enhances safety and enables cooperative driving, making roads more efficient and reducing the risk of accidents.
Power and Energy Management
IIoT can offer better solutions for power management in industries. Specific sensors can detect the environment and trigger to turn on/off control of lights, air conditioners, humidity controls, and liquid flow for efficient power management.
Example: EMMA energy management service on Proficloud, EMMA is the smart energy management service from Phoenix Contact. EMMA focuses on the energy manager as the user and is tailored precisely to their needs. With a simple, intuitive design, it provides a flexible spectrum of functions in the field of electrical energy and power data visualization for monitoring, analyzing, and evaluating this data.
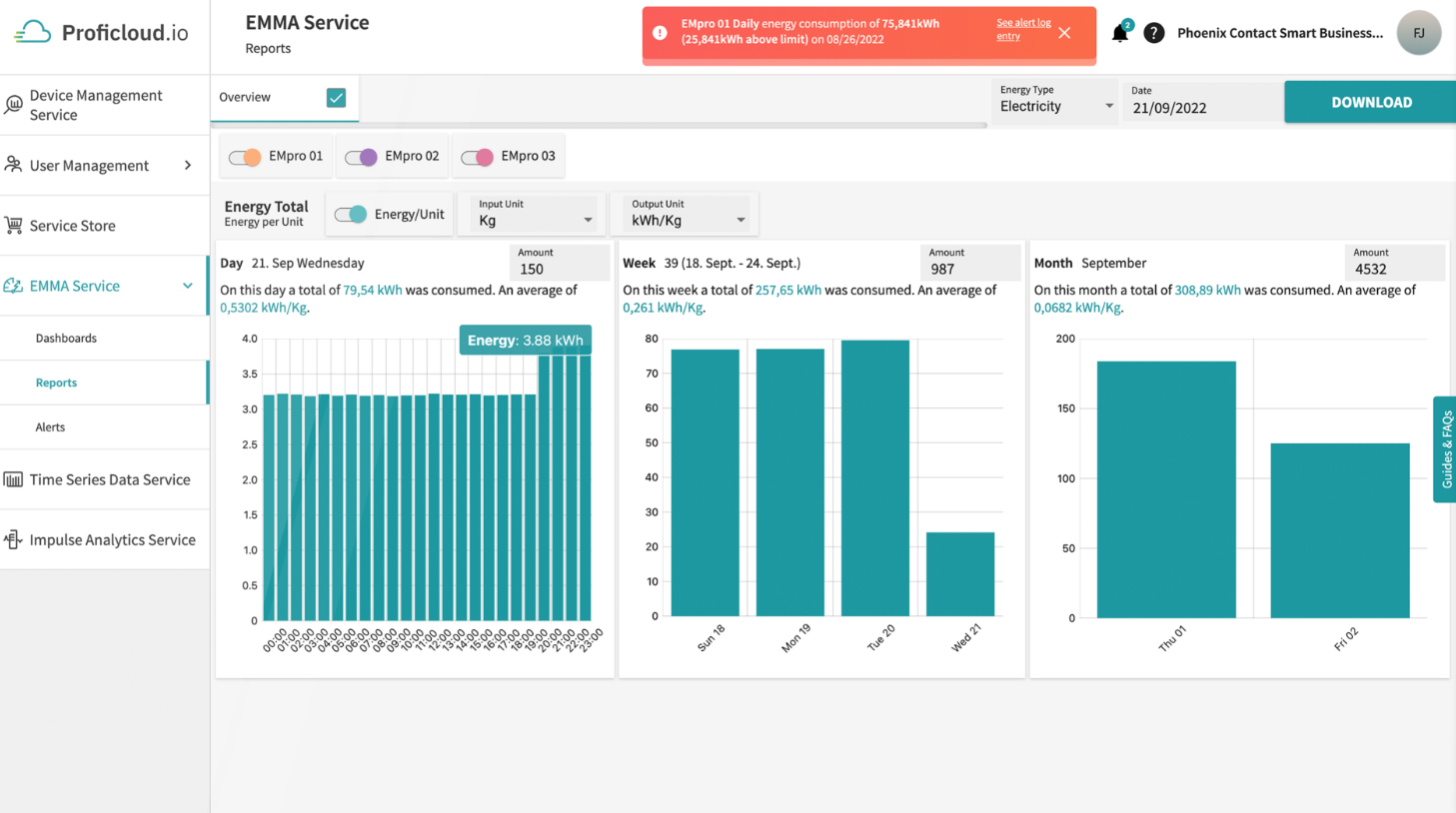
They use EMpro energy measuring devices for acquiring energy data and offer numerous options for communicating the data to higher level control and management systems.
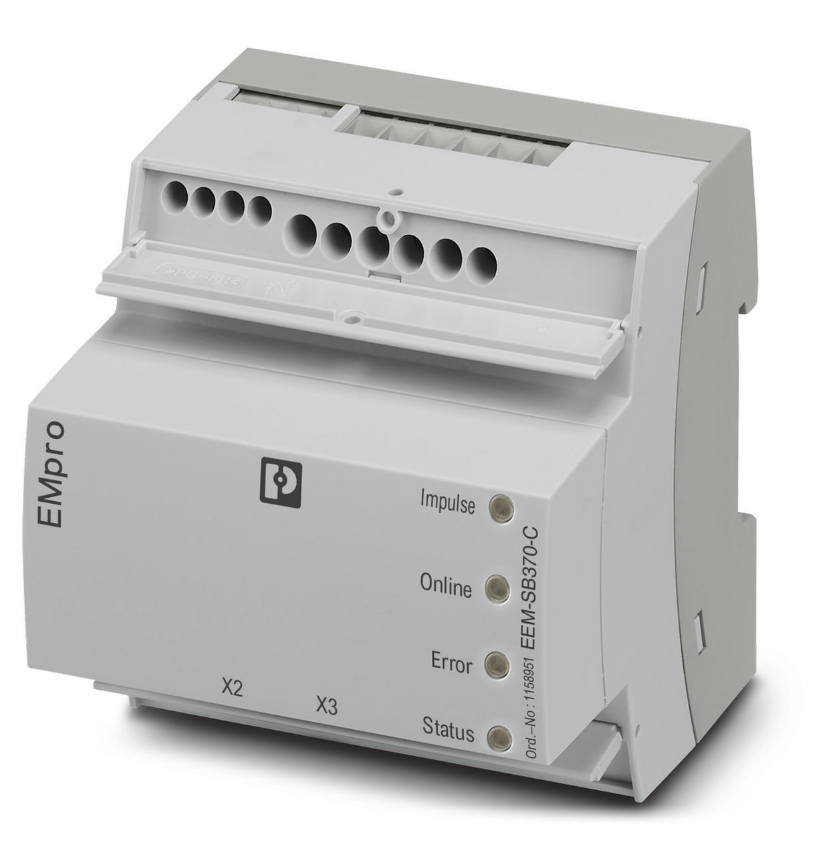
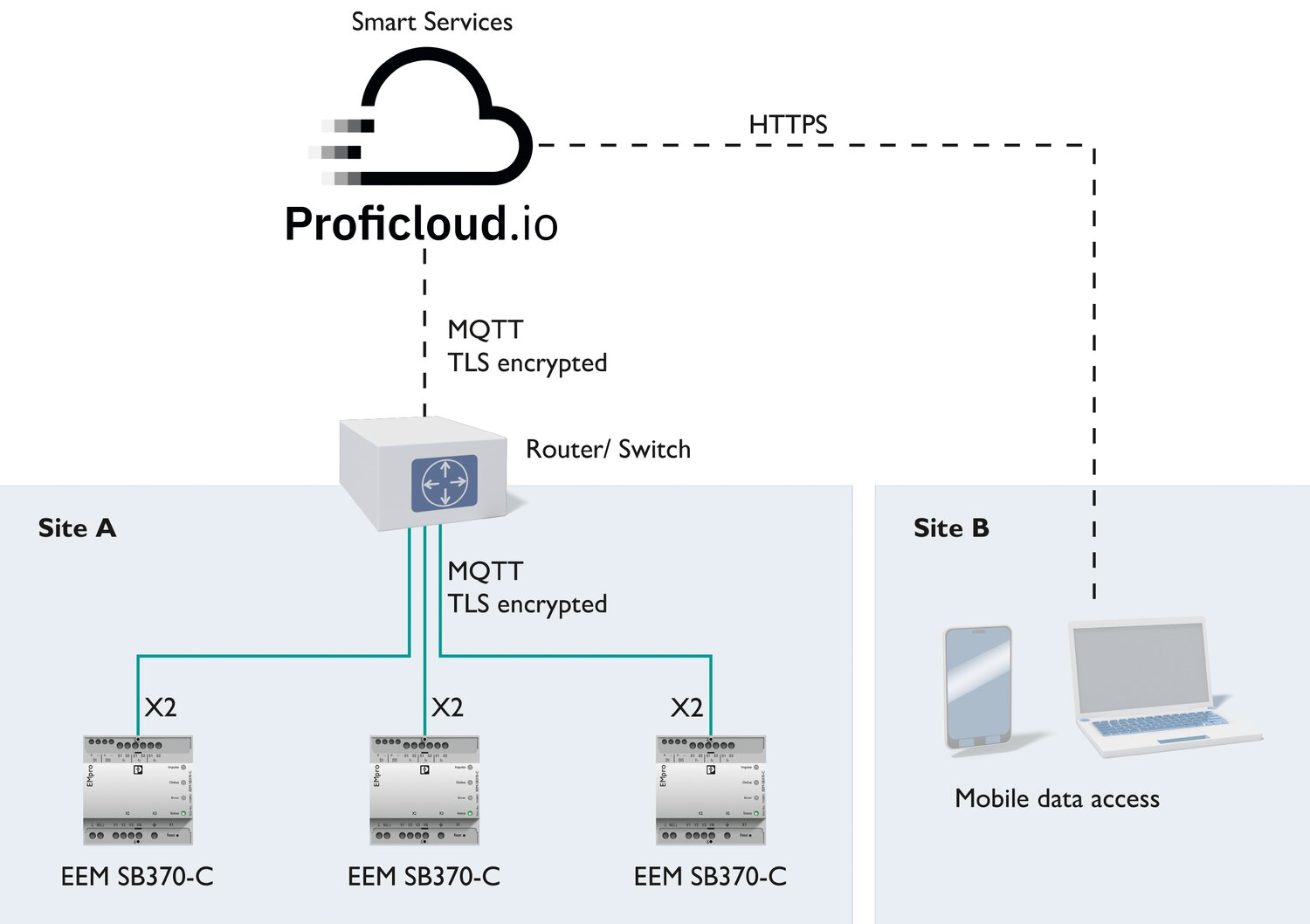
The advantages with the EMMA smart energy management service:
- High level user friendliness with a systemic overall concept with intuitive menu navigation and automated data transfer to the Proficloud.io.
- Energy and power data, targeted overviews independent of time or location via purpose oriented visualization systems.
- Constantly increasing value benefits for your energy management system with continuous, user-oriented further development.
- Secure communication between the device and cloud via TLS encryption.
- Device management for a clear overview of the applications.
Use Cases:
- Energy Consumption at active and passive times.
- Consumption at different assembly times.
- Energy consumption per manufactured piece.
- Optimizing power management.
Supply Chain Management
Supply chain management is a highly complex process that overlooks the entire lifecycle of a product, from raw materials to its final state. Application of IIoT provides much needed transparency, control, and automation. Such solutions allow employees to track goods in real time, monitor storage conditions, optimize routes, and locate goods within storage. Whenever a delay occurs, managers will be immediately informed to mitigate the situation. Additionally, IoT systems can predict traffic jams and deliver an optimal route to avoid any roadblocks.
Also one of the key benefits of IIoT in supply chain management is the ability to enhance operational efficiency across various stages of the supply chain. By connecting different components of the supply chain, such as manufacturing facilities, warehouses, transportation systems, and retail outlets, IIoT enables real-time data collection and analysis. This connectivity allows for seamless coordination and synchronization of activities, optimizing production, inventory management, and distribution processes.
For example, smart sensors integrated into manufacturing equipment can monitor performance, detect anomalies, and automatically trigger maintenance or repairs, reducing downtime and improving overall productivity. Additionally, IIoT enables predictive maintenance, where data analytics and machine learning algorithms can identify patterns and predict equipment failures before they occur, enabling proactive maintenance scheduling and reducing costly breakdowns.
Remote monitoring and control
Most factories and plants are located outside of cities, which forces managers to travel long distances to check up on the business. Industrial IoT applications include remote monitoring and control features that enable settings change and equipment operation. For example, if your system detects a gas leak, you can instantly initiate shutdown protocols and prevent a dangerous situation. Besides keeping accidents from happening, remote control can save huge costs since sending a technician to a remote location is costly.
On a larger scale, remote monitoring features allow managers to oversee and control several plants at the same time. Instead of assigning each area to a team of experts, companies can cut HR and operational costs. Having a consolidated overview of the entire business can also be beneficial in business decision making.
Employee and environmental safety
Operating heavy machinery can lead to workplace accidents and put your employees in serious danger. These can be prevented with the adoption of IIoT applications. Sensors can be placed on the workers to assess their perspiration, working technique, heart rate, temperature, and other metrics. Whenever a certain KPI goes outside the normal, managers will be automatically alerted to avoid hazards.
Digital Twin
Digital Twin is a detailed virtual representation of a physical object or system.Â
By using sensor data and data from IIoT enabled devices, digital twins can be used to monitor the behavior and condition of a system in real time, allowing companies to quickly identify potential problems or issues as they arise and take action.
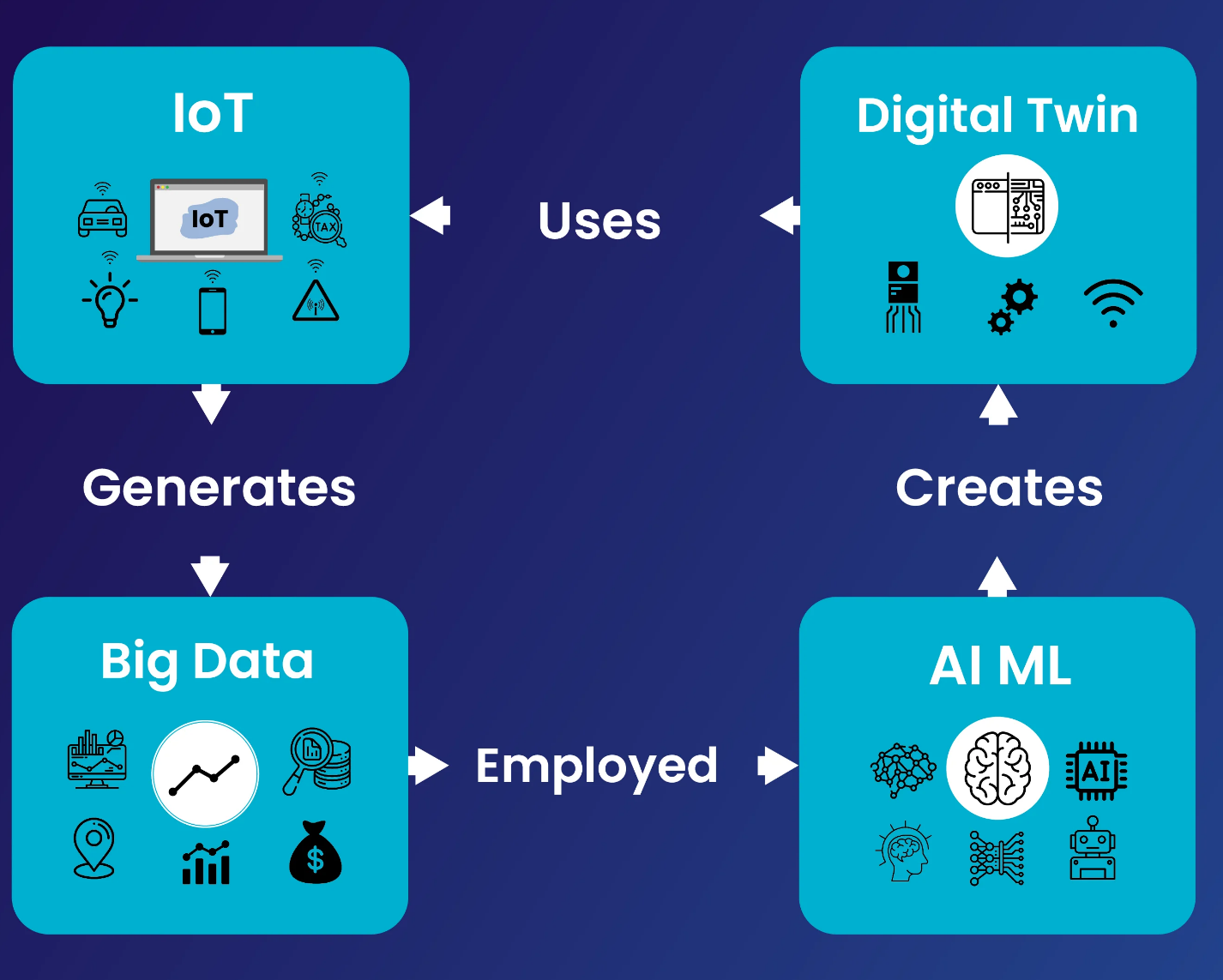
Simple Example:Â
Digital twin application for ABB robot using Unity3D softwareÂ
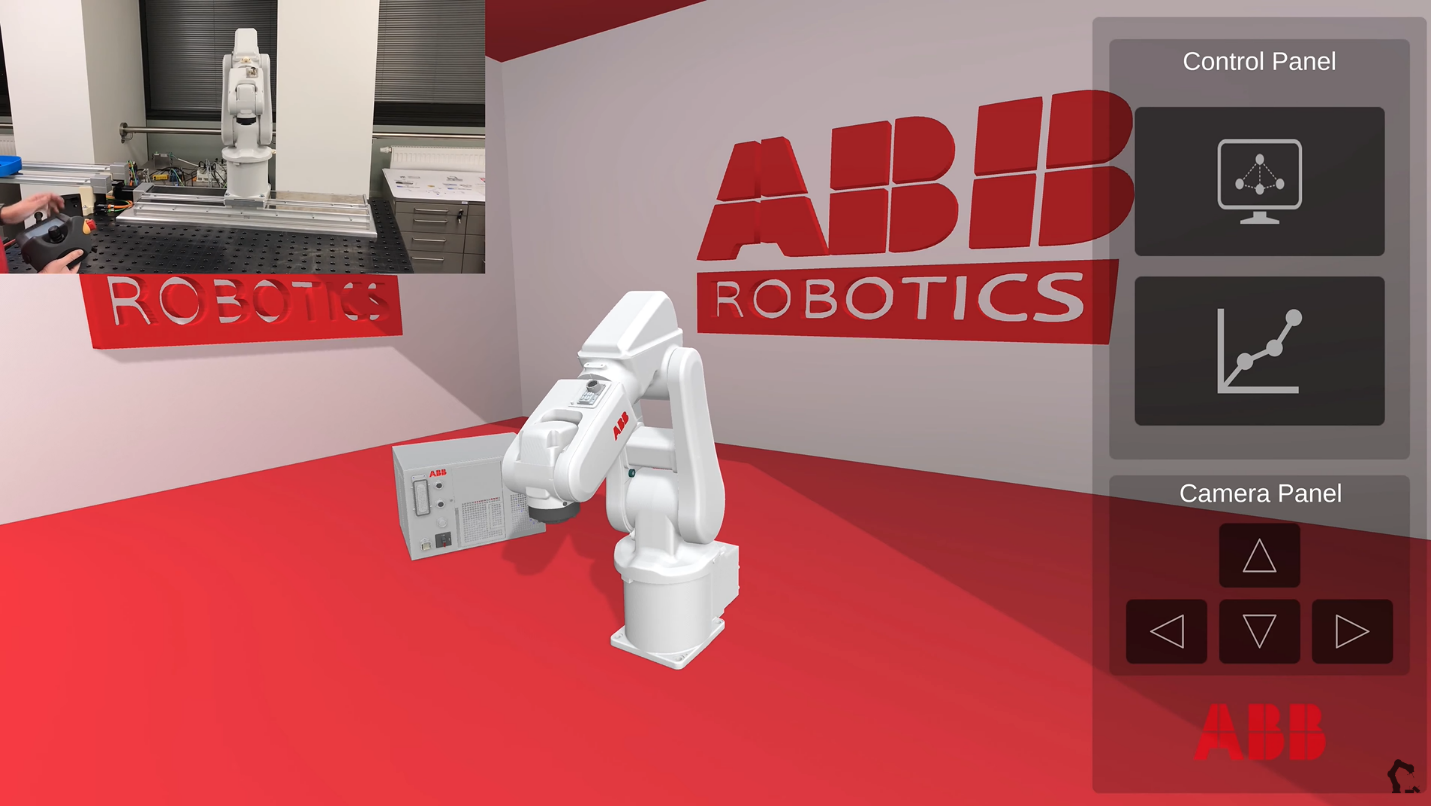
Predictive Maintenance
IIoT can be applied to prevent equipment failure and cut down on associated expenses. IoT sensors placed on equipment and vehicles can gather data on its performance and condition, such as vibrations, voltage, and temperature. These sensors detect and report any suspicious changes and slight performance degradations, giving technicians enough time to interfere and fix the issue before it impacts the production process.
This is a simple application of prediction maintenance for a motor, it is a simulation application let’s discuss it briefly:
We used a three factor for prediction:
- Temperature of Motor.
- Vibration of Motor.
- OEE values.
Second, because we don’t have real data for our AI model we created an excel sheet with 60K normal values and 40K abnormal values by using sklearn lib in python. We assume that normal values for temp, vibration and OEE are max 35 degree , max 0.2 , min 60.Â
This is sample for train dataset:
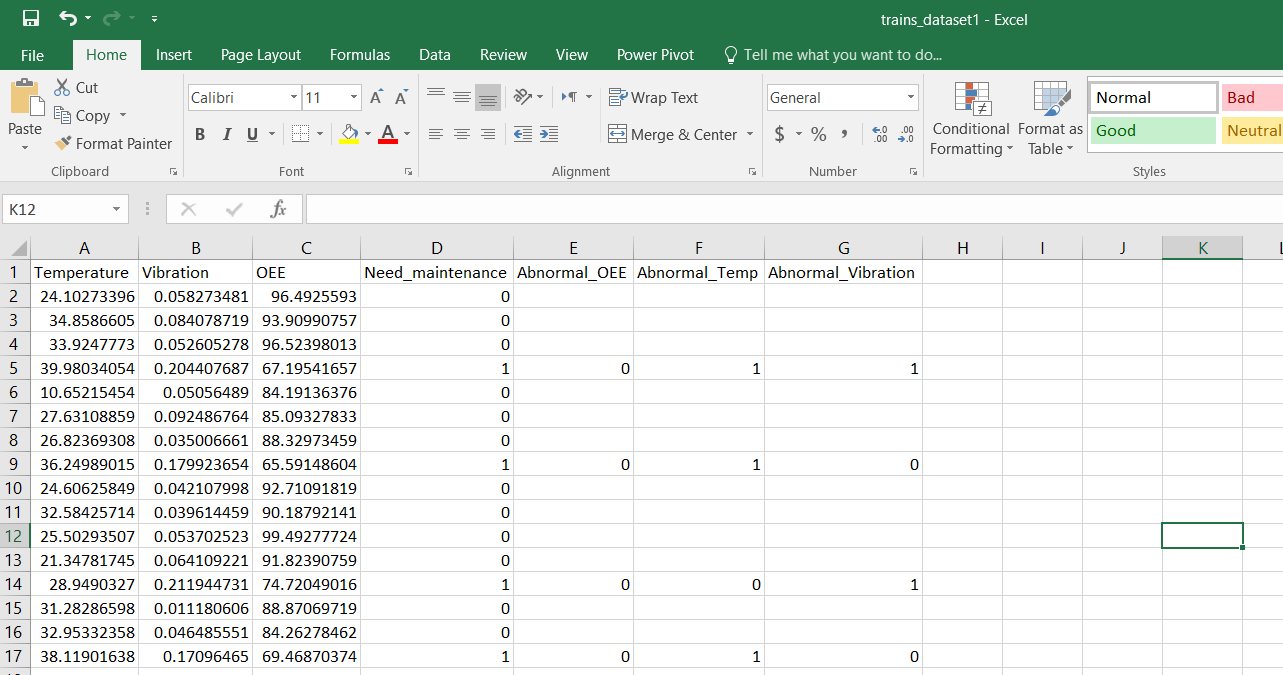
After creating a train dataset which simulate all past data for the motor during operationÂ
Next we Train an AI model using python with a train dataset.
Now we need real data which coming from the system but as we simulate it we input real data using Node-RED dashboard and save it in excel sheet directly:
This is sample for real data coming from Node-RED
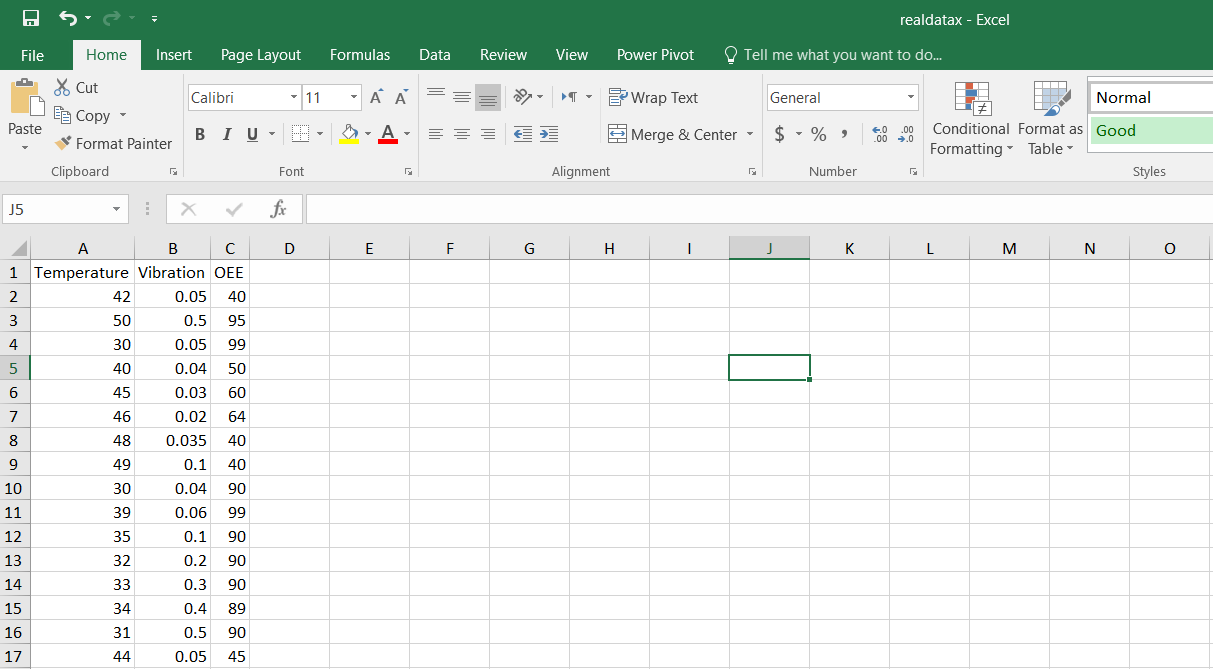
Now we load the trained model and the excel sheet with Real data to make the prediction according the trained model and the real dataÂ
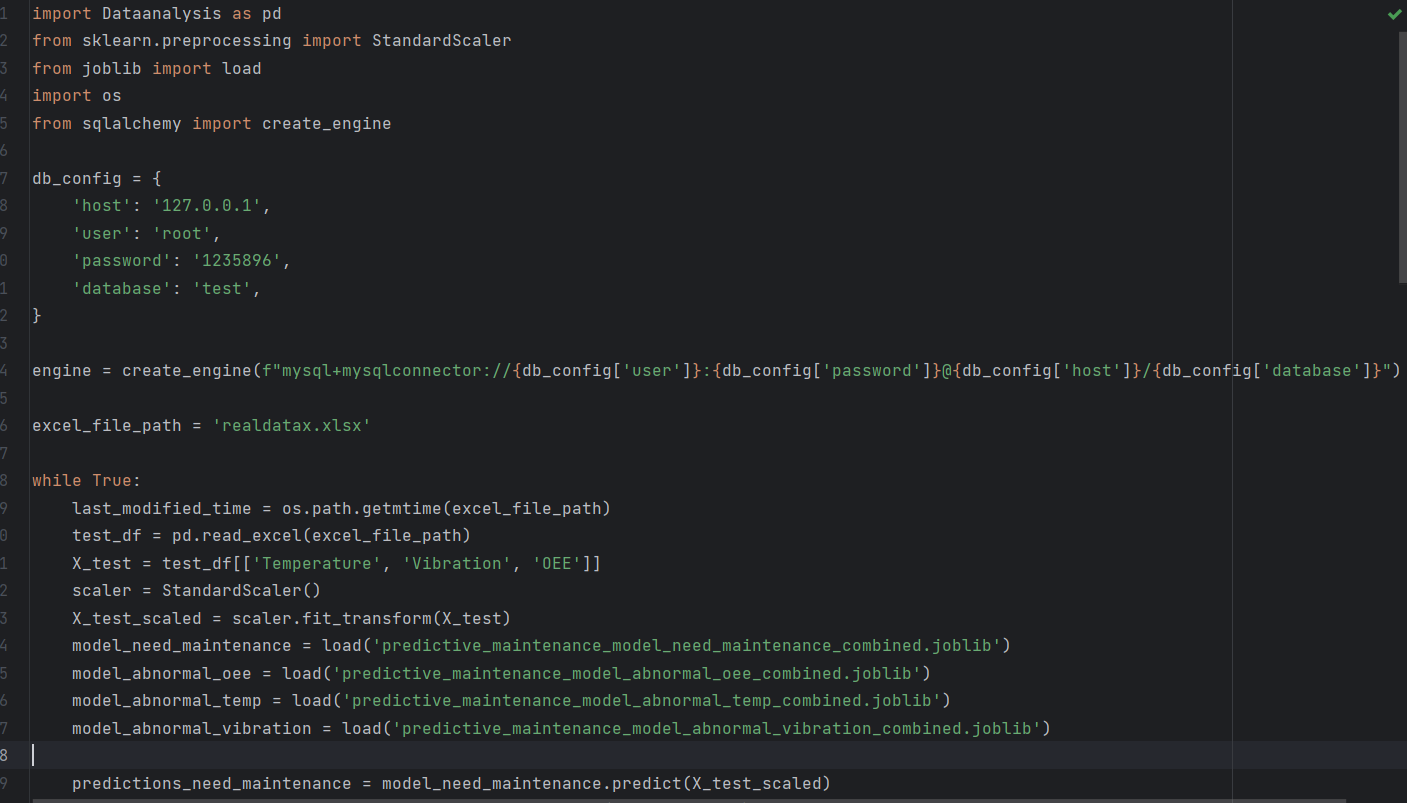
System run continuously and the result of prediction save in Excel sheet also in MySQL database and using Node-RED to send Email Notification with every prediction result in the system
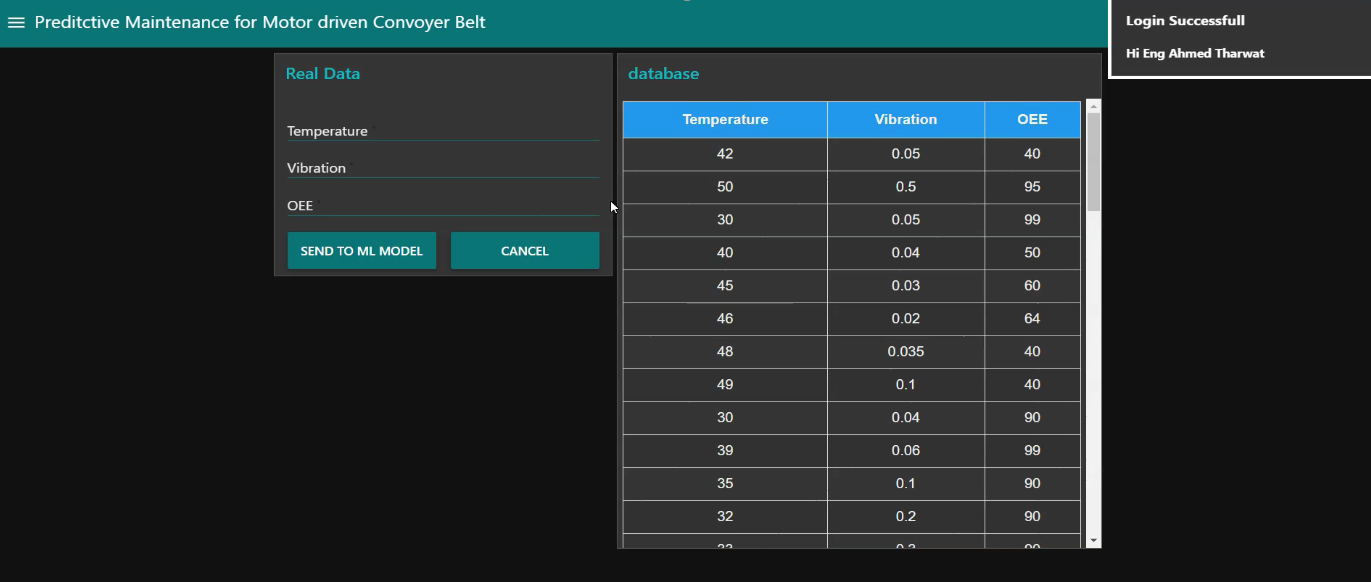
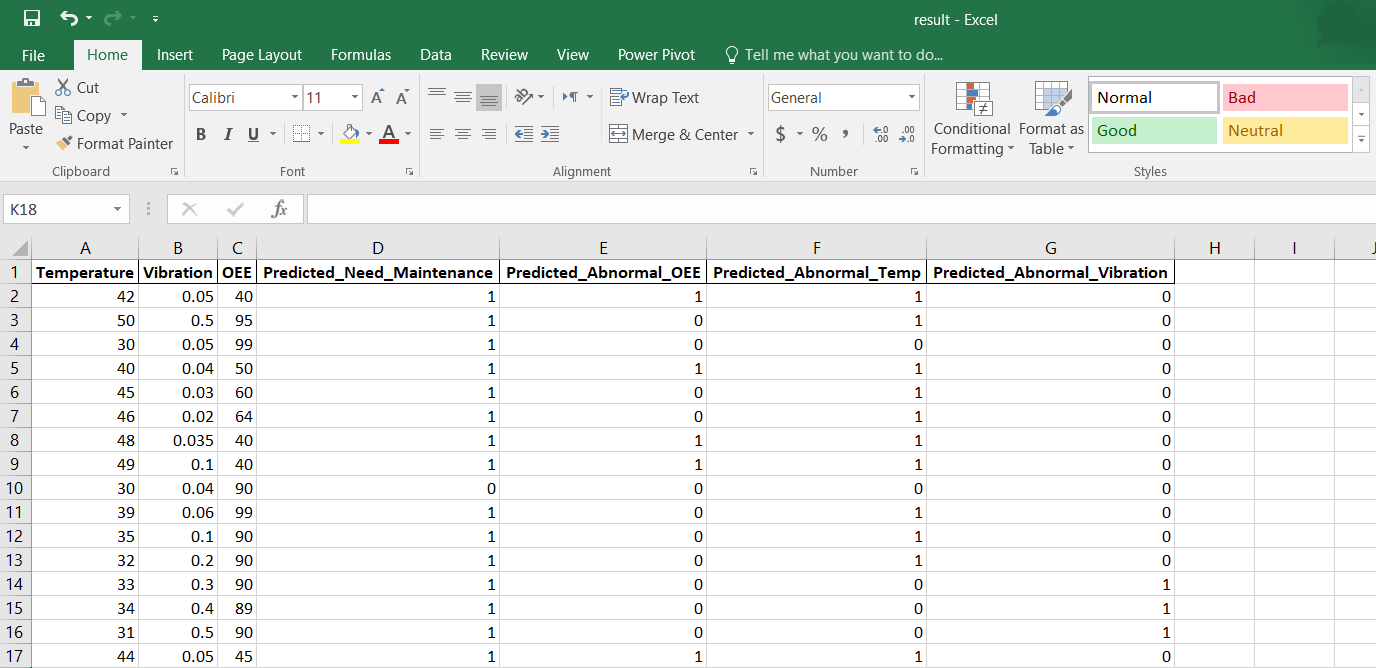
Note | you may find not correct prediction in the result but this because model need more training and train dataset must be updated with the new of system data with normal and abnormal values also I think we it will be more good if we use scheduling running time of motor in our train dataset
We can find a lot of companies uses IIoT Applications for its Business Like:
- Airbus: Smart Factory.
- Maersk: Route Optimization.
- Komatsu: Remote Monitoring.
- John Deere: Self Driving Vehicles.
- Amazon: Reinventing warehousing.
- KUKA: Connected robotics.
- Maersk: Intelligent logistics.
- North Star BlueScope Steel: Keeping workers safe.
- Magna Steyr: Smart automotive manufacturing
Conclusion
In conclusion, Industrial Internet of Things (IIoT) applications have ushered in a transformative era across various industries, revolutionizing traditional practices and paving the way for enhanced efficiency, productivity, and safety. From smart robotics to asset tracking, quality control, autonomous vehicles, power and energy management, supply chain management, remote monitoring, employee safety, digital twins, to predictive maintenance, the diverse applications of IIoT are reshaping the landscape of industrial operations.
‍